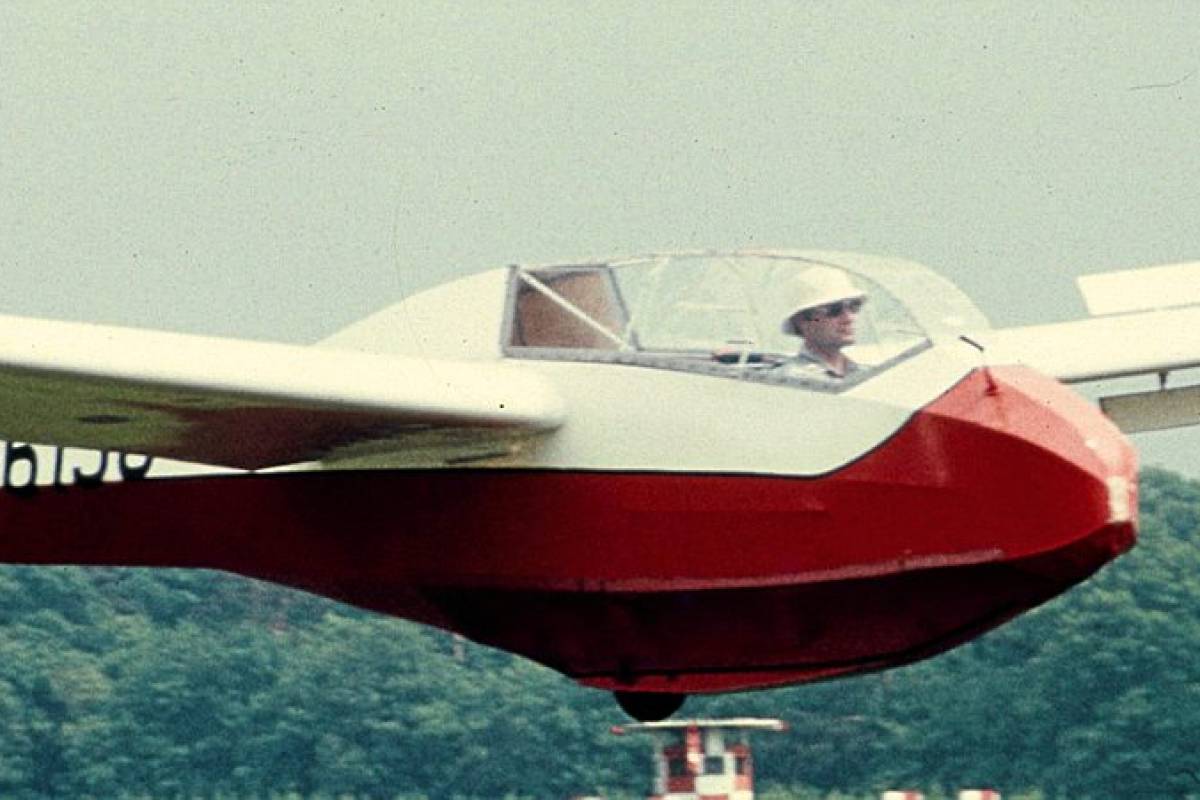
Der Bericht wurde am 15.12.2019
aktualisiert
Liebe Leser dieses Blogs,
wir haben derzeit leider eine echte Unterbrechung des Projektes durchzustehen.
Uns wurde schon vor einem Jahr mitgeteilt, dass wohl zur Jahresmitte 2019 mit der Renovierung der alten Werkstätten (große Garagenräume des alten Flughafens Broitzem aus dem zweiten Weltkrieg) in der Waldorfschule begonnen werden könnte. Die Bewilligung der notwendigen finanziellen Mittel zog sich dann aber noch hin. Jetzt steht fest, dass im Januar 2020 mit den Arbeiten begonnen werden kann.
Krankheitsbedingt von uns beiden und durch andere Anlässe konnten wir im letzten Monat und davor leider nicht mehr am Projekt arbeiten. Seit Ende November werden stückweise unser Sachen in die Unterkunft des Braunschweiger AeroClubs transportiert. Für den Rumpf wurde inzwischen auch eine Unterkunft gefunden, in der er in den nächsten Tagen gebracht wird. In wieweit dort weitergearbeitet werden kann, wird sich noch zeigen.
Ich werde hier wieder etwas schreiben, wenn es es weitergeht.
Bis dahin danke ich allen Spendern, Lesern und Verfolgern des Bergfalkeprojektes herzlich für Ihre Anteilnahme.
Ich wünsche uns allen einen zufriedenen Jahresschluss und viel Frieden, Gesundheit und Zufriedenheit für das Jahr 2020.
Bernd Junker
Der aktuelle Teil des Werkens erscheint bei jeder Aktualisierung an dieser Stelle und wird das nächste Mal hinten angefügt. Wenn Sie solange scrollen, bis rote Felder erscheinen, kommen Sie dort hin. Davor sind alle anderen gemachten Arbeiten chronologisch aufgeführt.
———————————-
Gefahr für die Kabinenhaube
Als kleinen Ersatz für die lange Pause ( Schulaktion für Lasse, Teilnahme von mir an einem Oldtimertreffen in Aalen Elchingen (war sehr interesssant, da dort auch ein Bergfalke war), krank mit viel Husten und reichlich Schnupfen und letztlich die Herbstferien) möchte ich euch außerhalb des Restaurierungsprozesses vom Bergfalken über eine laufende Untersuchung zum Thema „Reinigungsmittel auf Plexiglashauben (Acrylglas)“ berichten.
Angeregt durch die Aussage eines Werkstattleiters, dass er Aceton zum Reinigen der Hauben benutzt, habe ich eine Untersuchung über die Schädlichkeit von diversen Reinigungsmittel begonnen ….. und ich bin damit noch nicht am Ende !
Um es schon vorweg zu nehmen, alle bisher von mir getesteten Reinigungsmittel und Lösungsmittel führten nach der Behandlung des unbelasteten Plexiglases zu keiner sofort sichtbaren Beschädigung, das Acrylglas wurde sehr sauber ! Eine trügerische Sache !!
Mir sehr wohl bekannt ist aber die Langzeitwirkung von Aceton auf Acrylglas. Daher die Anregung zu der Untersuchung mit anderen Stoffen.
Jede Kabinenhaube aus Acrylglas hat durch den Herstellungsprozess noch kleine Restspannungen, die infolge Temperaturschwankungen im Betrieb mal größer und mal kleiner werden können.
Lösungsmittel, wie aufgebrachtes Aceton, beschädigen die Molekularstrukturen vom Acrylglas an der Oberfläche. Die Folge sind feinste Risse, die meist erst viele Monate nach der Behandlung zu sehen sind. Diese Risse werden im Laufe der Zeit immer mehr und die Sicht durch die Kabinenhaube wird bei einem ungünstigen Lichteinfall behindert.
Ich denke, dass solche feinen Risse von jedem schon mal gesehen wurden.
Damit die Untersuchung nun nicht Monate oder Jahre dauern soll, habe ich eine Vorrichtung gebaut, in der Streifen von 3 mm dickem Acrylglas unter hoher Spannung festgehalten werden.Wenn diese Streifen nun mit den Reinigungs- oder Lösungsmitteln benetzt werden, sind die Ergebnisse innerhalb von 10 Stunden zu sehen.
Bei Aceton kommen die kleinen Risse sofort und der 3 mm dicke Teststreifen bricht nach ca. 30 Sekunden
Durch die hohe Spannung im Plexiglasstreifen entstehen die Risse schnell innerhalb von Sekunden, Minuten oder erst innerhalb von Stunden. ….. Egal , das jeweilige Mittel hat die Haube beschädigt und diese Beschädigung ist nicht mehr rückgängig zu machen.
Bei folgenden bisher untersuchten Stoffen traten Risse auf :
- Aceton
- Sika Reinigungsmittel-5 (enthält Xylol)
- Waschbenzin
- Flugzeugbenzin
- redu Rain ( ein Mittel, dass nach der Beschreibung Glas- und Kunststoff-Flächen wasserabweisend machen soll. –> eigentlich ideal für die Oberflächenpflege eines Fliegers )
- Pronto Glanz-Pflege
- Glasreiniger von „Wintec“ (Autoglasscheibenreparateur)
- WD 40
- Caramba Oelfleck Entferner
Verlockend, aber ein für Plexiglas sehr agressives Mittel ! (Autoscheinwerfergläser sind heute oft auch aus Kunststoff hergestellt)
Die Untersuchungen gehen weiter und ich werde darüber auch berichten. Ich kann nur Jedem empfehlen, mal eigene Versuche mit Plexiglasresten von kaputten Hauben zu machen. Dazu das Plexiglasstück am Schraubstock einspannen und belasten. Das zu untersuchende Mittel auf ein Tuch geben und damit die Probe an der Einspannstelle länger benetzen.
Wenn ihr jetzt sagt, so ein Quatsch, ich reinige nur mit Wasser und Lederlappen, dann denkt bitte an den Fall in der Werkstatt, wo Dreck, Klebekram oder Farbe auf die Haube gekommen ist und man dies nun entfernen will. Man sucht etwas zum Abwischen , greift unbedarft ( vielleicht jetzt nicht mehr ) zu einem Reinigungsmittel, wischt den Dreck / Farbe ab und ist zufrieden, da alles nun wieder sauber ist …………..
Leider wird erst viel später bemerkt, dass die Haube feine Risse bekommt. Ob sich noch jemand an das „Attentat“ erinnern kann und das dann auch noch zugeben mag ???
Für intensive Reinigungen nur das von den Plexiglasherstellern empfohlene Material benutzen !!!!!
Eine gute Adresse ist : http://www.acrylglasprofi.de
DANKE für das Lesen.
Es geht demnächst weiter im Bergfalkeprojekt 🙂
xxxxxxxxxxxxxxxxxxxxxxxxxxxxxxxxxxxxxxxxxxxxxxxxxxxxxxx
Die letzten Arbeiten vom Donnerstag, den 12.09.2019
Neben der Montage der Lagerungspunkte (Knickstützen) für die Höhenrudersteuerstange wurden heute im Wesentlichen Putzarbeiten gemacht, d.h. die am letzten Donnerstag eingeklebten Bauteile wurden verschliffen.
Die drei Knickstützen der Höhensteuerstange wurden final mit Unterlegscheiben und Splinte montiert. Die angerosteten Montagestifte (Rohr) wurde abgeschliffen und prüniert.
Bei einem der unterschiedlich langen Montagestifte war die normale Unterlegscheibe zu dick. Mit einem Holzstück und einer darin eingefügten Schraube wurde die Unterlegscheibe aufgenommen und an der Schleifscheibe auf die notwendige Stärke abgeschliffen.
Die Sperrholzstücke an den hinteren Querkraftbolzen wurden an den Verklebungsstellen und gegenüber den Formleisten geschliffen.
Ebenso geschah dies mit den Klebestellen der seitlichen Verkleidungen und der vorderen Verkleidung. Kleine Unebenheiten , bzw. Vertiefungen wurden ausgespachtelt.
Zum Abschluss kommt der Rumpf dann immer wieder auf sein Ablagegestell.
Lasse zeigte mir dann noch eine von ihm ausgearbeitete Neufassung unseres Projektbloges, der demnächst zu besuchen ist ….. 🙂 Kleine Abstimmungen sind noch nötig ….
Nächsten Donnerstag werden wir den Spachtel verschleifen und kleine Anpass- und Ergänzungsarbeiten am Rumpf, den Sitzen, sowie der hinteren Bodenplatte vornehmen.
******************************************************************
Nach diesem Arbeitsplan geht es weiter:
Einkleben der Verstärkungsleisten unter dem hinteren Sitz.Einbau einer Leiste an der vorderen Sitzschale vorn.Einpassen von Zusatzhölzern an den Befestigungspunkten des hinteren Sitzes.Einbau einer Haltestange für das Drehen des RumpfesEinbau des Befestigungsbleches für die Antenne auf dem Baldachien.Vernieten der seitlichen und oberen Formleisten am Rumpf.Einkleben der Abdeckungen an den hinteren Querkraftbolzen und an den Seitenteilen im Cockpitbereich.Putzen der Klebsstellen und Montage der Halterungen für die Höhensteuerstange, Spachteln der Fehlstellen.- Verschleifen der Spachtelungen
- Bodenplatte vor dem hinteren Sitz
- Restarbeiten an den Sitzen.
- Einbau von Kufe und Rad.
- Montage der Steuerung.
- Weiterarbeit an den Instrumentenbrettern
- Fortsetzung des Bespannens von den Querrudern
- Bespannen des Höhenruders
- Bespannen des Seitenruders
Danke für das Verfolgen unseres Projektes 🙂
__________________________________________________________________________
Das zur Verfügung stehende Geld ist leider verbraucht. Über Spenden, auch kleinerer Art, würden wir uns sehr, sehr freuen, damit das Projekt daran nicht scheitert.
Das Spendenkonto für das Projekt wird von der Freien Waldorfschule Braunschweig e.V. geführt. Spendenbescheinigungen werden ausgestellt, wenn die Anschrift bekannt ist.
- GLS-Bank
- IBAN DE39 4306 0967 0015 9927 00
- BIC GENODEM1GLS
Bitte alle Spenden mit der Zweckbestimmung “Bergfalke” versehen und mir bitte auch mitteilen. DANKE b.junker@daec.de
—————————————————————————————————————–
Zum Projekt
Das 64 Jahre alte historische Schulsegelflugzeug Bergfalke II wird mit Hilfe von Schülern im Rahmen eines Schulprojektes an der Freien Waldorfschule Braunschweig sowie unter zeitweiser Mitarbeit von Schülern der Heinrich Büssing Berufsschule in Braunschweig restauriert.
_________________________________________________________________________
Das Projekt ist eine private Initiative aus der ehrenamtlichen Mitarbeit im Bundesausschuss KULTUR vom Deutschen Aero Club e.V. (DAeC).
https://www.daec.de/verband/ausschuesse/hauptseite-ba-kultur
Der Bundesausschuss Kultur wurde von Gerhard Allerdissen im April 2015 gegründet. Er war der Initiator der Unterschutzstellung historischer Luftfahrzeuge als Denkmal und regte auch die Charta von Braunschweig an.
Gerhard Allerdissen verstarb am 12. September 2017
_________________________________________________________________________
Veröffentlichungen durch Medien:
Juli 2017 : Gedanken und Artikel zum Erhalt von mobilen historischem Kulturgut sind in der Ausgabe 2/2017 der Fachzeitschrift RESTAURATOR im HANDWERK nachzulesen.
http://www.restaurator-im-handwerk.de/fileroot/rih22017web-kl.pdf
Da geht es nicht nur um Flugzeuge, sondern um alle technischen Verkehrsmittel, die der Mensch geschaffen hat. Hier der Link zu der Kopie eines Artikels über das mobile Kulturgut Luftfahrzeug:
Achtung: Durch Umstellung der Internetpräsentation des DAeC ist dieser Beitrag im immer noch nicht lesbar. Abhilfe soll hoffentlich noch folgen…. :-(((
Februar 2017: Die Sinnhaftigkeit der flugfähigen Erhaltung von historischen Flugzeugen wird in Artikeln der Zeitschrift MONUMENTE der Deutschen Stiftung Denkmalschutz erläutert.
http://www.monumente-online.de/de/ausgaben/2017/1/Interview/Interview.php#.WJMurPJSFVJ
In der Dezember-Ausgabe 2016 des AEROKURIER wurde über unser Projekt berichtet:
In der Braunschweiger Zeitung wurde das Projekt schon 2015 vorgestellt:
_________________________________________
Für das Schulprojekt Bergfalke werden weitere Institutionen und Privatpersonen gesucht, die diese Restaurierung unter Einbindung von Schülern, förderungswürdig erachten und mit Finanz-, Sachmittel und Dienstleistungen unterstützen möchten.
Das zur Verfügung stehende Geld ist leider fast verbraucht. Über Spenden würden wir uns sehr freuen.
Das Spendenkonto für das Projekt wird von der Freien Waldorfschule Braunschweig e.V. geführt.
- GLS-Bank
- IBAN DE39 4306 0967 0015 9927 00
- BIC GENODEM1GLS
Alle Spenden bitte mit der Zweckbestimmung “Bergfalke” versehen.
Die Spender erhalten eine steuerlich absetzbare Spendenbescheinigung, wenn ihre Anschrift bekannt ist.
Ich bitte um ein kurze Mitteilung, wenn eine Spende eingezahlt wurde. (b.junker@daec.de)
Falls Sie das Projekt mit einer Sachspende unterstützen wollen, bitte ich um eine Nachricht.
Text- und Projektverantwortlich: Bernd Junker ; b.junker@daec.de ; 0531 2361050 ; 0177 2361050
_________________________________________
Das Projekt wurde bisher mit Geldzuwendungen, Materiallieferungen und Dienstleistungen unterstützt durch:
- Private Spender
- Prof. Dietrich Hummel (Arbeitskreis Braunschweiger Luftfahrtgeschichte e.V.)
- Friedrich Franzmeyer (Arbeitskreis Braunschweiger Luftfahrtgeschichte e.V.)
- Renate und Dieter Smala-Stiftung (treuhänderisch verwaltet durch die Bürgerstiftung Braunschweig)
- Sandro Rutz (Besitzer einer LOM 57 „Libelle“ (DDR-Produktion))
- Mario Selss (Besitzer mehrerer historischer Flugzeuge)
- Jürgen Dreyer (Besitzer mehrerer historischer Flugzeuge)
- Akademische Fliegergruppe Braunschweig
- Ausbildungsverbund der Wirtschaftsregion Braunschweig/Magdeburg
- DLR Deutsches Zentrum für Luft- und Raumfahrt
- Fa. ALZ Auto Lackier Zentrum GmbH in Braunschweig
- Fa. Klamroth & Schwarz Metallbau GbR in Braunschweig
- Fa. Messer Cutting Systems GmbH
- Fa. Streiff & Helmold GmbH in Braunschweig
- Fa. Hilker Verpackungen in Braunschweig
- Fa. beju-technik in Braunschweig
- Fa. Plandienst
- Fa. IRSA Lackfabrik Irmgard Sallinger GmbH
- Fa. Swix-Sport GmbH (ToKo)
- Fa. Linde – Gas
- Fa. W. Max Wirth Kunststoff-Erzeugnisse
DANKE
für die Anerkennung dieses Schulprojektes und für die geleisteten Unterstützungen.
____________________________________________________
Der Anstoß zu diesem Projekt war der Nachklang durch das Verfassen der „Charta von Braunschweig“.
Über die „Charta von Braunschweig“ informieren Sie sich bitte unter dem Link:
https://www.daec.de/fileadmin/user_upload/files/2015/Charta_von_Braunschweig.pdf
In der von der FAI ( Fédération Aéronautique Internationale ) ratifizierten „Charta von Braunschweig“ sind die international verbindlichen Grundlagen für den fliegerischen Erhalt historischer Flugzeuge niedergeschrieben.
____________________________________________________
Das Schulprojekt
Hier ist der Bergfalke II von Christian Hülsheger aus Dülmen zu sehen, der uns freundlicherweise diese Bilder zur besseren Betrachtung eines Bergfalken II, zur Verfügung gestellt hat. Auch dieses Flugzeug wurde durch eine hervorragend gelungene Restaurierung vor der Vernichtung gerettet.
So ähnlich wird auch unser Bergfalke II mal aussehen.
Zur Restaurierung des Bergfalken II
So fing dieses Projekt an:
Das zweisitzige Schulflugzeug Bergfalke (Baujahr 1955) wurde nach 24 jährigen intensivem Vereinseinsatz vor 40 Jahren beim Aero-Club Braunschweig außer Dienst gestellt, ging in die sicheren privaten Hände von zwei Vereinsmitgliedern und sollte im Laufe der Zeit eigentlich grundüberholt werden. 2015 wurde aus wärmetechnischen Gründen die Decke der Werkstatt der Segelflugsparte des Aero-Club Braunschweig saniert. Die immer noch an der Decke hängenden Bauteile des Flugzeuges waren nun im Wege. Die Restaurierung des alten Bergfalken war leider nicht viel weiter vorangekommen. Die Verschrottung oder ein Verschenken wäre der nächste Weg gewesen.
40 Jahren lang hing der „abgelederte“ Bergfalke wohlverwahrt unter der Werkstattdecke der Segelflugsparte vom Aero-Club Braunschweig.
Der Rumpf besteht aus 0,5 mm dünnen Stahlrohren und die Flügel und Leitwerke sind aus Holz gefertigt. Im flugfertigen Zustand ist alles mit Stoff bespannt.
Die Flügel und die Leitwerke waren gut und trocken an der Werkstattdecke eingelagert.
Um das historische Flugzeug zu erhalten und den Inhalt der durch die FAI international anerkannten „Charta von Braunschweig“ auch hier in Braunschweig mit Leben zu füllen, wurden die hiesigen Schulen angeschrieben, um durch ein Schulprojekt die Restaurierung dieses Flugzeuges mit Schülern durchführen zu können.
Dabei soll den Schülern Einblicke und Fertigkeiten in die alte Handwerkstechnik des Flugzeugbaus in Gemischtbauweise (Holz und Stahlrohr), durch tätige Mitarbeit unter der Anleitung erfahrener Werkstattleiter, vermittelt werden.
Das eigentliche Ziel des Projektes, neben dem Wiederaufbau dieses historischen Flugzeuges, soll für die Schüler das Kennenlernen der Handwerkstechniken im historischen Flugzeugbau sowie das Durchhalten des manchmal mühsamen Weges, sein.
Die Notwendigkeit von Verständnis und Ausdauer, die Bereitschaft zum Lernen von gemachten Fehlern, die Sorgfalt bei der Tätigkeit der Restaurierung und die Bedeutung der Zuverlässigkeit in der Ausführung der Arbeiten sollen vermittelt werden.
Durch das große Interesse an der Umsetzung und besonders den mit praktischen Ausbildungsinhalten versehenen Lehrplänen der Schule sowie auch der Möglichkeit der Nutzung eines großen Werkraumes wird das Projekt an der Freien Waldorfschule in Braunschweig durchgeführt. Die Schule befindet sich auf dem Gelände und in den Gebäuden des alten Flughafens Broitzem …. welch ein Bezug zur Flugzeugrenovierung.
Ebenso konnte erfolgreich um die Mitarbeit der Heinrich-Büssing Berufsschule in Braunschweig geworben werden. Die Fähigkeiten und dortigen Lernziele im Umgang mit Metall werden für die Realisierung des Projektes benötigt, der Anhänger wird dann die große Aufgabe sein.
Das Schüler-Team an der Waldorfschule bestand im Januar 2016 aus :
Jonas Julian Norman Rico
und seit März ist auch ein zweiter Jonas dabei.
und nach Ostern ist Lucas dazugekommen
Herzlich Willkommen im Projekt
Das Schulprojekt wurde in der Presse bereits 2015 vorgestellt:
Am 15. Januar 2016 konnte nach einer Planungs- und Abstimmungsphase mit den Arbeiten begonnen werden.
Die Vorarbeit
Das Flugzeug besteht aus dem aus Metallrohren gefertigten Rumpf sowie den aus Holz gebauten Flügeln und den Seiten- und Höhenleitwerksteilen. Der Rumpf ist im Wesentlichen das Teil, was in der Waldorfschule bearbeitet werden kann. Die Flügel werden in der Werkstatt des Braunschweiger Aeroclubs renoviert. Dazu ist in der Schule kein geeigneter und abgesicherter Raum vorhanden. Die Leitwerksteile werden vielleicht auch in die Werkstatt der Waldorfschule kommen, z.B. für das Bespannen..
Damit der Rumpf während der übrigen Werkstunden nicht die Werkstatt belegt, musste zuerst eine Vorrichtung gebaut werden, um den Rumpf störungsfrei lagern zu können.
An dieser Wand soll der Rumpf gelagert werden.
Dazu wurde ein solider Kran aus Holzlatten, Tischlerplatten, Spanplatten und diversen Metallwinkeln, Schrauben, Bolzen und einer gespendeten elektrischen Winde hergestellt .
Aus der vorgefertigten 1:1 Zeichnung werden die Maße für den Wandkran abgenommen.
Das Krangestell lässt sich schon erahnen. Herr Hesse, Werklehrer der Waldorfschule, ist mit dabei und achtet auf den korrekten Bau.
Mit sehr soliden Dübeln wurde der Kran an der Werkstattwand befestigt. Ebenso wurden zwei wegklappbare stabile Auflagevorrichtungen gebaut und an die Wand geschraubt. Zwei in der Schule vorhandene Böcke für die arbeitsgerechte Lagerung des Rumpfes erhielten Rollen zur besseren Positionierung in der Werkstatt. Der Rumpf wiegt ca. 65 kg.
3. Februar 2016
Nach Fertigstellung des sehr erfolgreich von den Schülern absolvierten ersten gemeinsamen Arbeitsabschnittes, der Herstellung des Wandkranes und der Vorrichtungen zum Lagern des Rumpfes, konnte am 2. Februar der Rumpf des Bergfalken aus den Räumen des Aero-Clubs in die Waldorfschule geschafft werden und lagert nun an der Wand im Werkraum.
Da hängt er nun und wartet auf die weitere Bearbeitung:
Jetzt gibt es viel zu tun, so zum Beispiel :
- Ausbau aller Steuerungsteile und der Konturholzleisten
- Entlacken der Steuerungsteile und der Konturholzleisten
- Lackieren der Steuerungsteile
- Einbau neuer Lagerungen in die Steuerungsteile
- Überholung der Sitze und Fussbretter
- Entlackieren und Neulackieren des Rumpfgerüstes
- Einbau der Steuerungsteile und der Holzteile
- Bespannen des Rumpfes incl. Spannlack
- Montage der Kufenelemente und des Rades
- Lackierung
Beginn der Arbeiten am Flugzeug
12. Februar
Die Dokumentation der im Rumpf verbauten Steuerungsteile sowie danach deren Ausbau und die Entfernung der formgebenden Seitenleisten werden durchgeführt.
Zum Entfernen der Seitenleisten aus Holz werden die Nietköpfe einseitig abgefräst.
Der Werklehrer, Herr Hesse, hilft und schaut, dass es gut wird.
Dann wird der Niet ausgebohrt.
Ein Durchschlagen oder Durchdrücken ging nicht … 😦
Alles mühsam, aber erfolgreich.
15. Februar
Fast alle formgebenden Holzleisten, hier eine Seitenleiste im Bild, sind nun abgebaut und werden im nächsten Schritt von der Farbe befreit und in Sichtholzausführung mit Klarlack aufgearbeitet. Die im Bild zu sehenden, aus dem Gestell herausragenden Stützleisten (Holz) von den Randformleisten, wurden inzwischen auch schon entfernt.
Bei der engagierten Arbeit wurde von den Jungs beinahe der Beginn der nächsten Stunde -> Mathe verpasst. …. 🙂
19. Februar
So wie geplant, konnten die vorgesehenen Arbeiten durchgeführt werden:
- Fortsetzung des Abbaus der oberen formgebenden Holzleiste.
- Beginn der Farbentfernung von den ausgebauten Randformleisten.
- Reinigung der Rohre von Anbindungsresten an den Stellen der Stützleistenbefestigungen.
- Beginn mit dem Ausbau der Steuerungsteile.
Mit heißer Luft wird die Farbe von den Randleisten erweicht und mit dem Spachtel abgehoben.
Mit Sandpapier erhalten die Leisten dann wieder eine Holzoptik, die mit Lack konserviert wird.
Das Ausbauen der Steuerungsteile ist zum Teil eine fummelige Arbeit. Die Splinte sind aus den Kronenmuttern zu entfernen.
22. Februar
- Fortsetzung der Farbentfernung
- Fortsetzung des Ausbaus der Steuerungsteile
So haben wir es heute am Montag auch gemacht. Bis auf drei noch widerspenstige Bauteile ist der Ausbau der Steuerung fast abgeschlossen.
Das Entlacken und Schleifen der Holzleisten geht am Mittwoch (Sondertag … vielleicht auch bald normal im Projekt) weiter. Diese Holzarbeit ist dann auch der Übergang zum Rippenbau und den Schäftübungen am Sperrholz.
24. Februar
- Entlacken und Schleifen der Holzleisten.
- Ausbau der restlichen Steuerungsteile.
Mit reduzierter Mannschaft konnte nicht alles so geschafft werden, wie geplant, da auch restliche Steuerungsteile sich zum Teil nicht so leicht entfernen ließen, wie gedacht.
Alle Steuerungsteile wurden in Anordnung hingelegt und in einem Plan aufgezeichnet.
Die vor dem Ausbau aufgebrachten Aufkleber wurden entfernt und mit beschrifteten und mit Draht an den einzelnen Steuerungsteilen angebundenen Anhängern, versehen.
Die Dokumentation für den späteren Einbau ist nun vorhanden.
26. Februar
- Entlacken und Schleifen der Holzleisten.
- Auftragen von Farbentferner auf den Steuerungsteilen.
- Herstellung von Filzringen für die neuen Lager
Es wurde eine kleine Einführung in den kommenden Rippenbau gegeben und Baubeispiele gezeigt. Zur Vorbereitung dieser Arbeit werden in den nächsten Wochen sogenannte Nagelbretter hergestellt. Dies sind Bretter, in denen Nägel entlang der Rippenkontur gesetzt sind, damit dagegen formgenau die Kiefernleisten angelegt werden können. Mehr dazu, wenn es mit den Holzarbeiten los geht.
Die Arbeit unter Punkt 1 wird uns auch noch nächste Woche verfolgen. Da müssen wir halt durch, damit es gut wird.
Punkt 2 wurde durchgeführt. Das Abkratzen und dann das Strahlen erfolgt nächste Woche.
Bei Punkt 3 wurde geübt und leider festgestellt, dass das größte vorhandene Locheisen noch nicht groß genug war 😦 —> Montag neuer Anlauf mit anderem Werkzeug.
29. Februar
- Entlacken und Schleifen der Holzleisten.
- Abbürsten der gelösten Farbteile
- Herstellung von Filzringen für die neuen Lager
… mehr geschafft als gedacht. Die Fertigung der Nagelbretter konnte wegen ausgebliebener Vorarbeit durch Materialmangel noch nicht begonnen werden. Das Entfernen der angelösten Farbe geht bis jetzt zufriedenstellend.
Eine neue Entscheidung:
Das Stahlrohrgerüst wird selbst entlackt und neu grundiert und lackiert.
Die relativ guten Erfahrungen mit dem Abbeizen der Steuerungsteile und das derzeit fehlende Geld für eine Fremdvergabe gab den Entscheidungsanstoß. Der Vorteil ist auch eine Schonung des Rohrgestells, bedeutsam geringere Logistikarbeit mit Vorbesprechungen, Transport des Rumpfgerüstes sowie das Wegfallen der nicht einfachen Beschaffung des speziellen Strahlgutes aus Kunststoffgranulat. Zudem steht auch die Unsicherheit des wirklich guten Gelingens im Rahmen der geplanten Kosten im Raum.
Das Auftragen des Abbeizers wird aber nicht von den Schülern gemacht. Dies wird durch die Restauratoren selbst an einem Freitagnachmittag durchgeführt. Die Chemie kann dann auf dem Rumpfgerüst über das Wochenende wirken. In den weiteren Arbeitsstunden wird die gelöste Farbe abgezogen, die Rohre gereinigt und mit einer Grundierung geschützt. Wir werden uns von vorne nach hinten und vielleicht gleichzeitig von hinten nach vorn durchwurschteln.
Etwas mühsam … aber wir schaffen das … mit sturer Ausdauer geht alles … 🙂
2. März
- Entlacken und Schleifen der Holzleisten.
- Fertigung einer Ablage für die Leitwerke.
Abweichend vom Plan wurde heute neben dem Entlacken der Holzteile eine Ablagevorrichtung gebaut und auf einem Schrank festgeschraubt, auf dem die zu reparierenden Leitwerksteile gelagert werden können.
Eine kleine Präsentationswand gibt Besuchern Auskunft über das Projekt
4. März
- Entlacken und Schleifen der Holzleisten.
- Entlacken und Feinschleifen der Steuerungsteile
- Auftragen vom Abbeizer auf das Rumpfgerüstes (ohne Schüler).
Die Kontur-Holzleisten sind nun alle entlackt und geschliffen und bereit zur Lackierung. Das Entlacken der Steuerungsteile, nach dem Auftrag des Abbeizers, geht hervorragend. Mit dem Einsatz von Schleifpad und rotierender Messingbürste sehen die Bauteile wie neu aus.
Mit einem fast 150jährigen 2-Mann Team wurde nach dem Verlassen der Schüler das Rumpfgerüst mit Abbeizer eingestrichen. Eine stinkende Angelegenheit und arbeitstechnisch tröge langweilig, aber zu zweit war das dann, verbunden mit nettem „Klönschnack“, erträglich. Danke Manfred und willkommen im Projekt!
Dieser neue Projektpartner von Braunschweiger Aero-Club hat Bauerfahrung von Holzsegelflugzeugen und vielen Modellflugzeugen. Damit haben wir einen für die zukünftigen Holzarbeiten kompetenten Mitstreiter im Boot.
Besuch hatten wir heute auch von einem Mitglied des Braunschweiger Anti-Rost Vereins.
Am 2. März wurde in dem Braunschweiger Verein „Anti-Rost“ das Schulprojekt vorgestellt und es fand ein Gedankenaustausch über eventuelle gemeinsame weitere Aktivitäten um das Thema „Jugendliche und Senioren arbeiten zusammen in einem Projekt“ statt. Konkrete Vorstellungen liegen vor.
Die Einbindung, Beschäftigung und Ausbildung von Jugendlichen, auch aus der Gesellschaft der Flüchtlinge, in einer von Schule und Vereinszugehörigkeit unabhängigen Arbeitsgruppe ist angedacht.
Dies ist aber im wesentlichen eine Frage der politisch gesellschaftlichen Unterstützung durch entsprechende Institutionen aus der Stadt, die diese Projekterweiterung ermöglichen könnten.
!!!!!!!!!!!!!!!!!!!!!!!!!!!!!!!!!!!!!!!!!!!!!!!!!!!!!!!!!!!!!!!!!!!!!!!!!!!!!!!!!!!!!!!!!!!!!
7. März
- Entlacken vom Rumpf und den Steuerungsteilen
- Entlacken von Holzteilen
Wie geplant, so wurde gearbeitet. Wir haben jetzt Verstärkung von zwei weiteren Fliegerkameraden aus dem Braunschweiger Aero-Club bekommen.
Lutz und Rolf, herzlich willkommen im Projekt.
Die Farbentfernungsarbeiten an der Steuerung und besonders am Rumpfgerüst werden uns die nächsten Tage und Wochen noch reichlich beschäftigen. Eine blöde Arbeit ……..
Parallel dazu wird der Rippenbau mit den Nagelbrettern vorbereitet und bald kann mit Verleimungs- und Rippenbauübungen auch begonnen werden.
>>>>>>>>>>>>>>>>>>>>>>>>>>>>>>>>>>>>>>><<
9. März
- Entlacken vom Rumpf und den Steuerungsteilen
- Lackieren der Holzteile
- Entlacken von den aus Holz bestehenden Sitzen und Bodenbrettern
Wie geplant, so wurde gearbeitet.
Ein neuer Schüler – Jonas – hat sich der Gruppe angeschlossen. Es bleibt aber bei der Zahl von 5 Schülern, da ein Schüler leider schon lange nicht mehr teilnimmt.
Nun haben wir durch die hilfreichen Mitglieder des Braunschweiger Aero Clubs eine gemischte Mannschaft aus Alt und Jung.
Schön, dass es bei den Senioren viel zu erzählen gibt, da wird die Mühe der Farbentfernung am Rumpfgestell vielleicht nicht so bemerkt …
Vorschläge, diese Arbeit in die JVA (Justizvollzugsanstalt) Rennelsberg abzugeben, kamen dann aber doch ….
Der Aufdruck auf der Abbeizerdose verspricht 15 Farbschichten mit einem Rutsch zu erledigen. Uns würde es schon gefallen, wenn wenigsten zwei Schichten abgingen ….
Merke: Werbung ist halt immer ein Blendwerk der Hölle ….
Es muss bei fast allen Rohren nochmal nachgebeizt werden.
Die Steuerungsteile werden auch noch entlackt. Der Einsatz von Maschinen ist immer beliebt. Wie ging das bloß vor 60 Jahren, als derartige Geräte noch nicht verfügbar waren?
Die abgeschliffenen Holzleisten der Rumpfverkleidung wurden lackiert.
Das Leben eines Pinsels kann auch hart sein …………………..
Zum Trocknen wurden die sehr langen Leisten an einer vorher installierten Wäscheleine aufgehängt.
Am Abschluss der Arbeiten war der Rumpf wieder in seiner Wandposition, hier mit einigen zum Trocknen des Lackes aufgehängten Holzteilen.
An den Rohren sieht man schon etwas den Fortschritt der Farbentfernung.
>>>>>>>>>>>>>>>>>>>>>><<<<<<<<<<<<<<<<<<<
11. März
Entlacken vom Rumpf und den Steuerungsteilen.
- Schleifen der Holzteile.
- Auftragen von Abbeizer auf den aus Holz bestehenden Sitzen und Bodenbrettern.
- Auftragen von Abbeizer nach Unterrichtsschluss auf die nachzubearbeitenden Bereiche.
Wie geplant, so wurde gearbeitet.
Wir haben dazugelernt, dass ein nochmaliges Auftragen des Abbeizers das Säubern der Rohre sehr vereinfacht. Abstrahlen der Reste mit feinsten Mitteln ist zu aufwendig. Dennoch wird es noch ein mühsamer Weg werden, bis das Rumpfgerüst entlackt ist. Die Arbeit geht aber mit dem Oldie-Team und den Schülern noch gut gelaunt voran. Von den Senioren wird eine sehr gute Durchhaltestimmung ausgestrahlt.
Die nächste Woche sollen dann bereits sauber entlackte Abschnitte mit Grundierung geschützt werden.
>>>>>>>>>>>>>>>>>>>><<<<<<<<<<<<<<<<<<<<<<<<<<<
14.03.
- Entlacken vom Rumpf und den Steuerungsteilen.
- Entlacken der aus Holz bestehenden Sitzen und Bodenbrettern.
Wie geplant, so wurde gearbeitet.
Die Entlackung der Steuerungsteile ist abgeschlossen und die Bauteile werden nun extern lackiert.
Ein weiterer, sehr an der Restaurierung interessierter Senior ist heute im Projekt eingestiegen und hat fleißig Farbe mit abgekratzt.
Jürgen, herzlich willkommen im Projekt.
>>>>>>>>>>>>>>>>>><<<<<<<<<<<<<<<<<<<<<<<<<<<<
16.03.
- Entlacken vom Rumpf.
- Auftrag von Grundierung auf die entlackten Bereiche des Stahlrohrgerüstes.
Ganz so wie geplant konnte heute nicht gearbeitet werden, da die Schüler fehlten. Da wurde wohl letztens von uns nicht richtig zugehört ……
So wurde mit 4 Senioren eifrig weiter die Farbe vom Rumpfgerüst gekratzt und die schon perfekt gereinigten Rohre wurden mit einer Grundierung geschützt. Die Steuerungsteile wurden ebenso grundiert.
Diese Sektion vom Rumpfgerüst ist entlackt und mit Grundierung geschützt.
Die grundierten Steuerungsteile hängen zum Trocknen auf der Wäscheleine.
Nun geht es für zwei Wochen in die Ferien :-)) Neben den Schülern kommen die Senioren nun auch mal wieder in den „Genuss“ der Osterferien….. :-)) Am 4. April geht die Renovierung weiter.
>>>>>>>>>>>>>>>>>>>><<<<<<<<<<<<<<<<<<<<<<<<<<
04.04.
Die Osterferien waren schön :-))
- Entlacken vom Rumpf.
Heute nur weiteres Abkratzen und Abschleifen des alten Lackes. Ziel ist es, am Freitag wieder ein definiertes Stück Rohrgestell zum Grundieren fertig zu haben. Über das Wochenende kann der Lack gut härten und der „Duft“ verschwindet.
Eine neue Front beim Entlacken wurde aufgemacht. Wegen des Personalgedränges wurde auch vorne entlackt. Das wird den Vorteil erbringen, dass beim Lackieren dann die beiden Enden des Rumpfgerüstes lackiert sind und der Rumpf dann dort auf Auflagern gedreht werden kann. Es ist immer wieder erstaunlich und etwas ärgerlich, welche Stellen beim Lackieren eines Rohrgestells weniger Farbe abbekommen können. Da muss von allen Seiten gründlich geschaut werden.
>>>>>>>>>>>>>>>>>>>>>>>>>><<<<<<<<<<<<<<<<<<<<
06.04.
- alten Lack entfernen
- Prüfvorrichtung bauen
Das Entlacken geht von zwei Seiten weiter. Wir sind jetzt am zentalen Teil des Rumpfgerüstes angelangt wo viele Rohre kreuz und quer mit diversen Sonderhalterungen verbaut sind.
Das Gestell für die Aufnahme der Prüfvorrichtung wurde fertiggestellt.
08.04.
- Konzentriertes Entlacken
- Grundierung der entlackten Bereiche
Die Arbeiten wurden so wie geplant, durchgeführt. Das Wetter war gut, und so konnten die entlackten Gerüstteile grundiert werden. Lackiert wird vor der Werkstatt im Freien, darum muss das Wetter passen.
>>>>>>>>>>>>>>><<<<<<<<<<<<<<<<<<<<<<<<<<<<<<<
11.04.
- Konzentriertes Entlacken
Die Arbeiten wurden so wie geplant, durchgeführt.
Sehr konzentriert wurden auch die Knotenpunkte der Rohrkonstruktion bearbeitet. Diese Arbeit unterscheidet sich von der schlichten Reinigung des glatten Rohres durch die Komplexität der vielen Verschneidungen der zusammentreffenden Rohre und muss sehr sorgfältig ausgeführt werden.
Nicht wundern, weil so wenig Leute am Arbeiten sind. Die Bilder wurden nach Schulende gemacht, wo nur noch Rolf mit dabei war. Bei der Vielzahl von Personen wäre das Rumpfgerüst sonst nicht zu sehen gewesen. Der Übergangsbereich von fertig grundiert und noch in Arbeit ist hier gut zu sehen.
Beweisbilder der ganzen Mannschaft das nächste Mal 🙂 Rolf ist am „Polieren“
Am Haubenrahmen wurden so auch erstmal alle Knoten und Eckpunkte gereinigt.
Wenn der Haubenrahmen grundiert ist, wird daran eine Helling ausgerichtet, auf der dann der Rahmen für die offene Haube gefertigt werden kann.
Mit dem Haubenrahmen bekommt das Gerüst schon das Aussehen eines Flugzeugrumpfes. Alle noch nicht entlackten Rohre wurde wieder mit Abbeizer behandelt. Der vor Wochen aufgebrachte Abbeizer hatte nur mäßig gewirkt und das angelöste Farbzeug war auch wieder fester geworden…. :-((
Wenn man Optimist ist und Vertrauen in die weitere konzentrierte Arbeit hat, wird in der nächsten Woche das Entlacken des Rumpfgestells abgeschlossen sein.
>>>>>>>>>>>><<<<<<<<<<<<<<<<<<<<<<<<<<<<<<<<<<
13.04.
- Konzentriertes Entlacken
Die Arbeiten wurden so wie geplant, durchgeführt.
Die Landekufe wurde in das Rumpfgestell eingepasst.
>>>>>>>>>>>>>>>><<<<<<<<<<<<<<<<<<<<<<<<<<<<<<
15.04.
- Konzentriertes Entlacken
Die Arbeiten wurden so wie geplant, durchgeführt.
Das Lackieren konnte wegen der schlechten Witterung nicht durchgeführt werden. Es sieht im Fortschritt aber so gut aus, dass wie optimistisch angedacht, in der nächsten Woche das Entfernen des alten Lackes abgeschlossen werden kann. Die Schüler sind dann in den drei darauf folgenden Wochen zum sozialen Praktikum nicht in der Schule. In dieser Zeit erfolgt die Lackierung des Rumpfes mit Grundierung und Endlackierung. Ebenso werden alle Steuerungsteile dann entlackiert.
>>>>>>>>>>>>>>>>>>>>>>>>>>>>>>>>>>>>>>>>>>>>>>>>>>>
18.04.
- Konzentriertes Entlacken am Rumpfgerüst, Haube und Kufenelemente
- Erster Materialtest mit der Prüfvorrichtung.
Die Arbeiten wurden so wie geplant, durchgeführt.
Es drängt sich :
Der Werklehrer Herr Hesse, der Senior Jürgen und Julian, Jonas, Lukas und Jonas am Lackentfernen.
Rico und Norman hatten den Haubenrahmen in Arbeit.
Die Prüfvorrichtung wurde eingeweiht. Die Proben waren zwei Stück dreischichtiges Flugzeugsperrholz von 1 mm Stärke.
Es konnte gezeigt werden, dass es bei der Festigkeit auf die Anzahl und die Richtung der Holzlagen im Sperrholz ankommt.
Die Proben müssen leider sehr schmal ausgeführt werden, damit die Grenze der Waage von 50 kg nicht überschritten wird.
Wir werden wohl noch eine neue Waage beschaffen.
Die Festigkeit eines Schaschlikspieses konnte wegen Überschreitung der Last nicht festgestellt werden.
Weitere Untersuchungen werden folgen: Klebeverbindungen kommen auch auf den Prüfstand.
>>>>>>>>>>>>>>>>>>>>>>>>>>>>>>>>>>>>>>>>>>>>>>>>>
20.04.
- Entlacken vom Rumpfgerüst
- Bearbeitung der Kufe
Da die Schüler eine Lehrplanumstellung hatten und nicht anwesend waren, haben nur 3 Senioren sich am Entfernen des alten Lackes vergnügt.
Bei der Kufe wurden die seitlichen Sperrholzbeplankungen entfernt, um den Zustand des Kufenholzes begutachten zu können. Eine Renovierung ist notwendig.
>>>>>>>>>>>>>>>>>>>>>>>>>>>>>>>>>>>>>>>>>>>>>>>>
22.04.
- Entlacken von Rumpfgerüst, Haube und Kufenelemente
Die Arbeiten wurden so wie geplant, durchgeführt.
Leider wurde das Ziel der kompletten Entlackung heute nicht erreicht. Nächste Woche soll dies dann erreicht werden sowie auch die restliche Grundierung erfolgen.
>>>>>>>>>>>>>>>>>>>>>>>>>>>>>>>>>>>>>>>>>>>>>>>>
In der Zeit vom 25. April bis zum 13. Mai befinden sich die Schüler in einer 3-wöchigen Praktikumsphase.
>>>>>>>>>>>>>>>>>>>>>>>>>>>>>>>>>>>>>>>>>>>>>>>>>
Diverse Arbeiten wurden in dieser Zeit von den Senioren fortgeführt.
- Restliche Bereiche des Rumpfgerüstes entlacken.
- Grundierung des Rumpfgerüstes.
- Endlackierung des Rumpfgerüstes und der Steuerungsteile.
Vom 2. bis zum 6 Mai war die Schule und damit die Werkstatt geschlossen.
Die Fortführung der Renovierungs- bzw. Rippenbaumaßnahmen begannen am Montag, den 23. Mai.
>>>>>>>>>>>>>>>>>>>>>>>>>>>>>>>>>>>>>>>>>>>>>>>>>
22.04.
Sondereinsatz: Manfred hat den ausgemusterten Schrank von seiner Enkelin gebracht.
Gemeinsam wurde das immer noch gute Stück aufgebaut und wird fortan für die Aufbewahrung von Kleidung und Arbeitskittel sowie auch Materialien und der Steuerungsteile des Flugzeuges genutzt.
23. Mai
- Projektbesprechung und Planung der weiteren Arbeiten.
- Vorbereitung der Arbeitsbretter für den Rippenbau
Der weitere Ablauf des Projektes wurde besprochen. Die Arbeiten der überschaubar nächsten Stunden werden sich mit dem reinen Holzbau befassen. Nach Vorlagen wird der Bau von zwei verschiedenen Rippen praktiziert. Anfangs wird es eine einfache Rippe aus dem Bereich hinter dem Holm und vor einem Querruder sein. Für die Rippe (33) aus dem Nasenbereich eines Flügels müssen hingegen die äußeren Leisten vorgebogen werden.
Zur Vorbereitung der zum Bau notwendigen Nagelbretter wurden die Papierzeichnungen mit einseitig klebender Folie auf einfache Spanholzbretter aufgezogen. Die Folie dient neben der Fixierung der Zeichnung auch der Verhinderung des Festklebens des später eingesetzten Klebstoffes.
Auf die Gefahren und in die sachgerechte Nutzung an der Schleifscheibe wurde hingewiesen und das Schleifen der für das Nagelbrett notwendigen Holzklötze geübt.
>>>>>>>>>>>>>>>>>>>>><<<<<<<<<<<<<<<<<<<<<<<<<<<<<<<<<<
25. Mai
Arbeiten in drei Gruppen: Jede Gruppe hat zwei Schüler mit einem Betreuer.
- Fertigung der Nagelbretter für den Rippenbau
- Beginn des Zuschneidens der Holzleisten
- Grundieren des Rumpfes
Die Nagelbretter für die einfache Rippe wurden hergestellt und die einzufügenden Holzleisten zugeschnitten.
Beim der Ausfertigung der Nagelbretter wurden unterschiedliche Anbringungen der Stützklötze vorgenommen. Die Ergebnisse wurden gemeinsam betrachtet und kommentiert. Alle Ausfertigungen sind brauchbar, nur einige sind zu komplex und aufwendig gestaltet worden.
Auch der uralte Spruch der Handwerksmeister: „Der ganze Hammerstiel ist bezahlt“ fiel. Ganz ganz früher wurde der Faustkeil benutzt, dann der Hammerstiel erfunden und nun gilt es, das Gefühl im Umgang mit dem Hammer bei richtigem Anfassen des Hammerstiels an seinem Ende zu lernen und zu üben, um zielsicher und dosiert die Masse des Hammerkopfes ins Ziel zu bringen. Dies zu können, muss wirklich geübt werden!
Am Freitag werden alle Vorbereitungen zum Verleimen der Holzleisten in den Nagelbrettern abgeschlossen sein und die Verleimungen der Leisten kann erfolgen.
Das Rumpfgerüst wurde fast fertig grundiert.
Im vorderen Bereich müssen noch zwei Rohre ausgetauscht werden, deswegen fehlt dort der Lack.
Wer sich für die Arbeit und die Probleme beim Entlacken eines Rumpfgerüstes näher interessiert, kann mich gerne anschreiben, es wurden Fehler gemacht und viele Erfahrungen gesammelt, die gerne weitergegeben werden.
27. Mai , 29. Mai und 1. Juni
- Zuschneiden der Holzleisten
- Fertigung der Knotenabdeckungen
- Verleimen
Die begonnenen Arbeiten bei der Fertigung der Nagelbretter wurde abgeschlossen und die für den Bau notwendigen Leisten wurden zugeschnitten und eingepasst.
Das Verleimen der Leisten und der Eckversteifungen geschieht in dieser Übungsphase mit Ponal-Express. Sicherheitsvorkehrungen, wie für die Verleimung mit AERODUX notwendig, sind somit nicht nötig.
An kleinen Sägen werden die Leisten zugeschnitten
und an der Tellerschleifmaschine angepasst.
Der Zusammenbau beginnt.
Es entstehen viele Übungsrippen
Aus für die Größe der Scheibe passig zugeschnittenen viereckigen 1mm Sperrholzplättchen mit mittig gebohrtem kleinen Loch werden mit einer einfachen Vorrichtung an der Tellerschleifmaschine die runden Eckversteifungsscheiben durch Drehen hergestellt. Diese Kreiselemente werden mit der Schere in zwei Halbsegmente zerschnitten.
Nach dem Aushärten des Leims werden die Rippen aus dem Nagelbrett genommen und die andere Seite wird an den Knotenpunkten der Leisten mit halben Scheiben aus Sperrholz versehen.
Manches steht noch über, was später abgeschliffen wird. Zum Abschleifen der eventuell minimal überstehenden Versteifungen an der Ober- und Unterseite ist der handgeführte Schleifklotz zu nutzen. Die Schleifscheibe kann bei wenig Erfahrung schnell zuviel wegnehmen und dann ist die Kontur verdorben. Größere Überstände, wie hier im Bild die Leisten an den Stirnseiten, werden mit einer feinen Säge abgesägt und verschliffen. Das Abschleifen mit der Maschine sollte nur bei gewonnener Erfahrung und Können erfolgen.
Gepresst wurde hier mit Hilfe eines aufgelegten Brettes und als Gewicht benutzte Pflastersteine. Dabei ist aber aufzupassen, dass das mit Gewichten beschwerte Abdeckbrett beim Auflegen nicht die Eckversteifungen verschiebt. Die andere Möglichkeit des Fixierens ist ein leichtes Annageln der Plättchen mit kleinen dünnen Nägeln.
3. Juni
- Fertigstellung der gebauten Rippen
- Herstellung der Nagelbretter für die Nasenrippen
- Biegen von Holzleisten
Die Arbeiten konnten, so wie geplant, durchgeführt werden.
Die Leisten für die Oberseite und Unterseite der Nasenrippe müssen vorgebogen werden. Dazu werden die Holzleisten in kochend heißes Wasser gelegt und anschließend weiter im Wasserbad über Stunden bis zur Verarbeitung gelagert.
Die nun biegeweichen Leisten werden in einer der späteren Kontur etwas überangepassten Vorrichtung eingespannt und müssen in diesem Zustand trocknen.
Eine ungewässerte Leiste würde bei der vorgenommenen Biegebeanspruchung brechen oder wenn gerade nicht, eine zu große Spannung in die Rippe bringen. Es dauert lange bis sich im trockenen Holz eine Spannung abgebaut hat. Nachträgliche Rippenverformungen sind dadurch möglich.
Im trockenen Zustand haben die Leisten dann die gewünschte Formgebung und können in den Nagelbrettern für die Nasenrippen ohne größere innere Spannungen eingebracht werden.
Die laufenden Arbeiten befassen sich mit der Herstellung der Rippen vor und hinter dem Flügelholm und der weiteren Verwendung dieser gebauten Rippen für die Herstellung von Flügelsegmenten.
Es werden von jedem Schüler je 3 Rippen gebaut.
Die erste Rippe ist ein reines Übungsstück zum „Fehlermachen“. Fehler sind zuerst sehr willkomen, da daran vieles zu erklären ist. Bei den weiteren gfleichartigen Arbeiten sollten die bisher gemachten Fehler aber nicht mehr auftreten, sonst gibt es „Mecker“. Es wird Aufmerksamkeit und Lernbereitschaft erwartet.
Von den drei Rippen kann sich jeder Schüler eine Rippe mit nach Hause nehmen, wenn er es möchte. Aus den anderen Rippen werden Flügelsegmente gebaut, an denen dann das Bespannen mit Stoff und das Aufbringen von Sperrholz (Nasentorsionskasten) gezeigt und geübt werden soll.
Hierbei wird auch das Schäften (kraftschlüssiges Verbinden von Holzteilen ohne Aufdickung ) von Sperrholz gezeigt und reichlich geübt.
6. Juni
Es fand kein handwerkliches Arbeiten statt.
Es wurde in den 45 Minuten eine umfängliche Bestandsaufnahme der bisher geleisteten Arbeiten und Produkte sowie das Arbeitsverhalten in dem Projekt gemacht und manches auch kritisch angesprochen und diskutiert. Die Schüler wurden auch ermahnt, den Mut zu haben, sachliche Kritik an den lehrenden Senioren zu üben. Dies muss gleich geschehen und darf nicht erst nach Wochen gesagt werden.
Zu Beginn Fehler zu machen ist gut, es wird darüber geredet und das Warum und Wieso nochmal erklärt. Ganz wichtig ist dabei, dass wirkliches Verstehen eintritt. Da ist nun auch jeder Schüler gefordert, dieses Verstehen aus den Ausbildern heraus abzurufen und nachzufragen bis es „klick“ macht. Das Ziel einer Ausbildung ist verfehlt, wenn später der Schüler bei einer Nachfrage Aussenstehender sagt: Das haben die uns so gesagt ……………
Große Einigkeit beim Thema „Entlacken des Rumpfes“. Das Abkratzen der Farbe wurde als reichlich „doofe“ Arbeit von allen, auch den Senioren, bewertet. Da sind wir nun aber endlich durch und das Rumpfgestell erhält nach der stattgefundenen Grundierung bald die endgültige Lackierung. Die jetzige Arbeit an den Holzteilen ist hingegen sehr erfrischend und eine interessante Herausforderung, die vielleicht schon eher Spass machen könnte.
Die Arbeiten für die folgenden Werkstunden umfassten:
- Fertigstellung der gebauten Rippen
- Bau weiterer Nasen-Rippen
- Biegen von Holzleisten
Während der Sommerferien vom 23. Juni bis zum 3. August werden alle Flugzeugteile aus der Waldorfschule in der Vereinswerkstatt des Aero-Club Braunschweig gelagert.
Aktuelle Situation im Juni 2016 in der renovierten Segelflugzeugwerkstatt.
Die Flügel des Bergfalken, die nicht in die Werkräume der Waldorfschule passen, sind in der Werkstatt der Segelflugsparte des Braunschweiger Aeroclubs im Weinbergweg zur Aufarbeitung hineingebracht worden. Die Werkstatt ist während der Flugsaison leer und die Renovierungsarbeiten können hier ungestört vorgenommen werden. Die frisch gebackene Abiturientin Anika, Segelfliegerin im Verein, wird Rudolf Müller bei den Arbeiten helfen und dadurch einen Einblick in das Handwerk des Holzflugzeugbaus erhalten.
Die kritische Befundung der Flügelstruktur ist der Beginn der Restaurierung. Hier ist Rudolf Müller mit geschärften Blick im Einsatz zu sehen.
Weitere Berichte über die Arbeiten in der Werkstatt des Vereins sind weiter unten im Blog zu finden.
Der letzte Werktag in der Schule vor den Sommerferien war Montag, der 20. Juni.
An diesem Tag fand in den 45 Minuten ein Vortrag vor den Schülern und weiteren Zuhörern statt.
Herr Zhipeng Zhai, Student aus China, hielt in deutscher Sprache einen Vortrag auf PowerPoint über sein Modellbauprojekt „Horten 33“ im Maßstab 1:10 und 1:5 sowie über den Werkstoff BAMBUS, der in Europa bisher meist nur im Garten als kleine Pflanze vorkommt oder auch in Stockform andere Pflanzen eine Stütze gibt.
Er erklärte Bauweisen von Flugzeugen und berichtete über Vorstudien für das geplante Projekt „Rekonstruktion des Nurflügelmotorseglers Horten 33“.
Das Flugzeug Horten 33 ist nach dem Krieg in reiner Holzbauweise in zwei Mustern in Deutschland hergestellt worden. Derzeit hängen Reste davon im Museum.
Im Vortrag wurden die überragenden Festigkeiten von Bambus gegenüber den heimischen Hölzern und auch die Möglichkeiten der Herstellung von Sperrholz oder Schichtholz aus den bis zu 0,3 mm dünnen Bambusfurnierblättern präsentiert.
Bambus ist ein extrem schnell wachsender weltweit vorkommender Rohstoff, der noch ein großes Potential im Einsatz bei technischen Objekten, von Gebäuden bis hin zu Flugzeugteilen haben kann. Die Möbel- und Parkettindustrie beginnt derzeit mit der Nutzung, mehr allerdings noch aus optischen Aspekten.
Die ringförmigen Stämme eines Bambus werden bei der Aufbereitung zur Nutzung zu Leisten geschnitten und auch zu sogenannten Leimholzbindern verarbeitet, die dann direkt als Tragbalken verwendet oder zur Herstellung von Furnierblättern genutzt werden können.
XXXXXXXXXXXXXXXXXXXXXXXXXXXXXXXXXXX
Status 12. August 2016
Die Sommerferien sind vorüber, ein neues Schuljahr hat begonnen und ein reduziertes Team hat sich für die weiteren Arbeiten am Bergfalken bereitgefunden.
Mit dabei sind :
Julian Norman Rico
Den nicht mehr beim Projekt mitmachenden Schülern sei herzlich für die Mitarbeit gedankt. Das ganze Schulprojekt ist ein Versuch der Restaurierung eines Flugzeuges mit der Hilfe von Schülern. Da diese Mitarbeit aber nicht in einer freiwilligen Arbeitsgruppe durchgeführt wird, sondern ein ausgesuchter Schuluntericht im Werken ist, ist es durchaus verständlich, wenn nicht eine besondere Beziehung zum Fluggerät entsteht, andere Projekte vielleicht interessanter scheinen oder auch weniger anspruchsvoll sind.
Nach Absprache mit dem Werklehrer Herrn Hesse, werden die Arbeiten aber erst nach den Herbstferien wieder aufgenommen, da in den letzten Sommermonaten im Aussenbereich der Schule noch ein größeres Bauprojekt erstellt werden soll. Wir werden auch nach Beginn der Fortführung der Renovierungsarbeiten dem Außenprojekt bei guter Wetterlage die erste Priorität geben.
Durch die erfreuliche Aufstockung der Arbeitszeiten auf 3 Schulstunden am Montag und mit 2 Stunden am Freitag werden wir nun effektiver bei der Renovierung arbeiten können.
XXXXXXXXXXXXXXXXXXXXXXXXXXXXXXXXXXXXXXXXXXXXXXXXXX
Das angebotene Mitfliegen in einem Segelflugzeug hat Julian genutzt.
Julian meldet : Alles top …… Aufregung ??
Startbereit beim Braunschweiger Aero-Club auf dem Flughafen in Waggum
Auf geht´s …………………………………. dem Himmel entgegen
Es war ein schöner Sonntag, leider war nur schönes Wetter.
Die beiden Flüge waren nicht sehr lange, da die Thermik (Aufwind) an diesem Tag durch die hohe Wolkenabdeckung und der damit geminderten Sonneneinstrahlung nicht gut war.
Ein ausgiebigerer Thermikflug wird nachgeholt !
XXXXXXXXXXXXXXXXXXXXXXXXXXXXXXXXXXXXXXXXXXXXXXXXXXXXXX
15.August
Der Rumpf wurde aus der Werkstatt des Aero-Clubs wieder in den Werkraum der Waldorfschule verbracht.
Abfahrt vom Fliegerhof
Dort wird der Rumpf sowie die bisher gebauten Strukturteile für eine Präsentation während der 40 Jahrfeier der Waldorfschule (1. bis 10. September) ausgestellt.
Am 10. September besuchten viele ehemalige Schüler und Schülerinnen die Unterrichts- und Werkräume ihrer Schule. Die Präsentation des Schulprojektes „Renovierung Bergfalke“ zum 40 jährigen Bestehen der Freien Waldorf Schule in Braunschweig wurde sehr gut aufgenommen. Über 50 Personen besuchten während der Zeit von 3 Stunden das Projekt Bergfalke in der Werkstatt und waren sehr angetan, dass solch ein Projekt an der Freien Waldorf Schule in Braunschweig durchgeführt werden kann. Das Interesse war sehr groß und manche ehemalige Schüler und auch Schülerinnen haben es bedauert, dass sie nicht auch bei solch einem Projekt als Schüler dabei sein konnten.
Begeistertes Zuhören und großes Interesse wurden erfahren. DANKE dafür
Eine von den Schülern gefertigte einfache Vorrichtung zur Demonstration und Bestimmung der Festigkeiten von Materialien wie z.B. Sperrholz , wurde vorgeführt.
Verschiedene gefertigte Flügelrippen zur Lehre und Übung des Flugzeugbaus. Das Beplanken mit Sperrholz und das Bespannen mit Stoff folgt demnächst.
Die kleine Präsentation des Schulprojektes in der Werkstatt
In der nächsten Zeit werden Adapter für die beiden Enden des Rumpfes hergestellt, die ein Drehen des Rumpfes beim finalen Lackieren ermöglichen.
Dazu eine sehr gute Nachricht:
Vom ALZ, dem Auto Lackier Zentrum in Braunschweig haben wir die Zusage der kostenfreien Lackierarbeit des Rumpfgerüstes zur Unterstützung unseres Projektes erhalten. Das Lackieren wird dort von Auszubildenden durchgeführt.
DANKE
Leider konnte aus gesundheitlichen Gründen nicht, wie vorgesehen, am Projekt weitergearbeitet werden. Für die Lackierarbeiten muss das Rumpfgerüst noch die Aufnahmeadapter an den beiden Rumpfenden bekommen, damit der Rumpf beim Lackieren gedreht werden kann.
____________________________________________________________
31.Oktober
Es geht am Projekt weiter. Es wird aus gespendeten Sperrholzplatten eine Kiste gebaut, in der später entweder die geschlossene Haube oder die Cabriohaube gelagert werden können.
Zuerst wir die Kiste aber als eine solide Basis für eine Helling zum Bau der Cabrio-Haube dienen.
Aus den Zeichnungsmaßen mussten die Zuschnittmaße bestimmt werden.
Aus den vorhandenen Sperrholzplatten mussten Teilplatten geschnitten werden, da die Platten nicht das gesammte notwendige Maß hergaben. Die Platten müssen zusammengesetzt werden. Wie wird die Schäftung mit einbezogen ?
Nachdenken ist angesagt. Die Aufgabe wurde von den Schülern gemeinsam gelöst.
Herr Hesse, unser Werklehrer, schneidet die Platten auf das errechnete Maß
Dann kann mit dem Schäften begonnen werden. Das klappte dann auch gut. Die Bandschleifmaschine half dabei. Später wollen wir das Schäften auch mit Sperrholz von 1 mm Dicke üben, dann aber von Hand mit einem Schleifklotz.
4. November
Die Werkstatt war schön warm. In den 90 Minuten konnten wir sehr erfolgreich die vorgefertigten Platten mit angedicktem Epoxidharz verkleben. Schichtweise auf einer mit Folie geschützten Basisplatte erst die vier Deckelplatten (aus 2 mal 4mm wurden 8mm gemacht), dann die Bodenplatte sowie darauf die beiden Seitenplatten verklebt und gestapelt und immer wieder Folie dazwischen, damit bloss nicht die Platten unkontrolliert irgendwo zusammenkleben.
Die Plattenteile wurden mit einem langen Baulineal ausgerichtet und mit kleinen Drahtstiften auf die jeweils untere Platte festgeheftet.
Hier wird von Julian das überschüssiges Harz entfernt
Zum Schluss wurde alles gut mit den verfügbaren Schraubzwingen sowie Bretter und Latten verpresst. Die 90 Minuten Arbeitszeit waren gut ausgefüllt.
Ich bitte, die schlechte Qualität der Bilder zu vergeben. Es war leider nur mein einfaches Mobiltelefon verfügbar :-((
7. November
Die Bretter für die Kiste wurden verputzt und mit Eckversteifungsleisten versehen. Die Leisten wurden aufgeleimt, geheftet und von der anderen Seite vernagelt.
14. November
Der Zusammenbau der Kiste klappte gut. Die vorgefertigten Teile für die Wände und den Boden passten und wurden mit Leim, Nägeln und Schrauben zusammengefügt.
Julian in the box
Der Deckel musste indes um 4 mm in der Breite korrigiert werden, da er sonst zu genau gepasst hätte. Die Scharniere und die Verschlüsse wurden angepasst und werden endgültig am nächsten Freitag verschraubt. Griffe brauchen wir wohl auch noch.
Die Kiste ist schon erschreckend groß. Die Haube passt knapp, aber gut hinein. Die Kiste wird demnächst erst als steife Basis für die Cabrio-Helling dienen und später der geschützte Aufbewahrungsort der geschlossenen Haube sein.
———————————————————-
18. November (90 Min.)
Mit einer durch Krankheit reduzierten Mannschaft wurde an der Kiste mit der Montage der Scharnier- und Verschlussteile weitergearbeitet. Die Basisplatte für die Helling wurde vorbereitet. Die Anbringung von Drehvorrichtungen am Rumpf wurde an einer Seite abgeschlossen, am Rumpfende muss diese aber nochmal überarbeitet werden, da die Schwerpunktlage für eine drehende Rumpflagerung beim Lackiervorgang noch nicht gut ist.
21. November (135 Min.)
Nur mit Julian wurde heute gearbeitet. Die neue Drehaufnahme am Heck wurde montiert. Leider ist der Schwerpunkt doch noch nicht genau getroffen worden. Mit externen Zusatzgewichten wird das aber leicht auszugleichen sein. Zum Bau der Helling wurde ein Abdruck der alten Haube auf dem Rumpf erstellt. Somit werden die Verwerfungen des alten Haubenrahmens nicht auf die Helling für die Cabrio-Haube übertragen. Da es nicht regnete, konnte dann endlich der Rumpf zur Lackiererei ALZ in Braunschweig gebracht werden.
Der Lackiermeister Herr Heuneke von ALZ und Julian in der Lackiererei. Dort wird vor Ort noch die Schwerpunktlage zum ausgeglichenem Drehen korrigiert. Leider wieder ein mieses Bild meines Mobilphones, die Kamera lag in der Werkstatt :-((
XXXXXXXXXXXXXXXXXXXXXXXXXXXXXXXXXXXXXXXXXXXXXXXXXXXXXX
Die sehr erfreuliche Spende und Lieferung von den sehr teuren Schwenkkugellagern für die Steuerung, haben wir erhalten.
DANKE
XXXXXXXXXXXXXXXXXXXXXXXXXXXXXXXXXXXXXXXXXXXXXXXXXXXXXX
25. November (90 Min.)
Die Kiste wurde mit allen Beschlagteilen fertiggestellt, umgedreht und gleich als Basis für die Helling benutzt.
Mit dem Bau der Helling wurde begonnen. Der geschlossene Haubenrahmen dient als Vorlage. Die vorher am Rumpf gemachten Konturabdrücke sind gut zu sehen.
Das Lackieren wurde durchgeführt.
Das sieht eigentlich gut aus. So ein Rohrgestell ist aber sehr schwierig zu lackieren, damit alle Seiten der Rohre gleichmäßig beschichtet werden.
________________________________________________________
28. November (135 Min.)
Die Helling für die Cabrio-Haube wurde nach kleinen Umbauarbeiten fetiggestellt.
Für den Transport des Rumpfgestells auf dem offenen Anhänger von der Lackiererei zur Werkstatt wurde eine Transportvorrichtung zum Schutz des Lackes gebaut.
Mit der Überholung der Kufe wurde begonnen und die beschädigten Holzstrukturen abgeschliffen. Neues Eschenholz wird anschließend aufgeleimt.
Die fertige Helling nach kleinen Umbauten.
05. Dezember
Da wir das Rumpfgestell wegen Nacharbeiten noch nicht in der Werkstatt haben, wurde mit den vor Monaten erstellten Rippen weitergearbeitet und begonnen, diese hinter einem Holm liegenden Rippen, zu einem Verbund zusammenzuleimen.
Das sind reine Übungsstücke, um das Bespannen von Flügelstrukturen zu zeigen. Der Holm ist natürlich nicht echt und geleimt wurde mit Ponal. Für das Demonstrieren reicht das völlig aus und bedarf keiner Sicherheitsmaßnahme.
Fertig verleimt
Noch nicht verleimt, nur hingestellt.
09. Dezember
Heute wurde in der Waldorfschule nicht im Projekt gearbeitet. Es gab leider beim Lackierer einen Schaden am Rumpfgestell, der in der Segelflugwerkstatt vom Braunschweiger Aero-Club wieder schweißtechnisch behoben wurde. Die Behebung hat leider viel Arbeit und Zeit gekostet. Hier sei ein ganz großer Dank an Fliegerkamerad Carsten Charlet vom LSG Schäferstuhl (Salzgitter) ausgesprochen, der sehr kurzfristig als lizensierter Flugzeugschweißer uns helfen konnte. Ebenso möchte ich Nikolas Betz für die schweißtechnischen Vorbereitungen danken. Nikolas befindet sich noch in der schulischen Ausbildung und würde gerne als aktiver Segelflieger nebenbei auch die Flugzeugschweißerlizenz erwerben wollen.
Für diese Schweißarbeiten benötigen wir noch ein dafür sehr geeignetes Schweißgerät vom Typ MINITHERM HA. Eine entsprechende Sachspende würde unseren verfügbaren Finanzen sehr helfen. … Bitten wir mal den Weihnachtsmann ……. 🙂
Flugzeugschweißer gibt es nur sehr wenige und da möchte ich im Projekt auch diese Ausbildung gerne unterstützen. Für den Erhalt der historischen Flugzeuge ist der Nachwuchs an lizensierten Flugzeugschweißern ganz wichtig. In diesem Zusammenhang ist der Kontakt zu Carsten Charlet sehr willkommen. Carsten hat sich bereiterklärt, die Schweißausbildung von Nikolas aktiv zu unterstützen.
DANKE
Zu Schweißen gibt es einiges, da die komplette Fußsteuerung nicht mehr vorhanden ist, und neu gebaut werden muss. Dies geschieht Anfang 2017.
In der nächsten Woche werden am Rumpf in der staubfreien Werkstatt vom Aero Club die restlichen Lackarbeiten nach dem Schweißen, durchgeführt und wir hoffen, den Rumpf bald zur weiteren Ausrüstung in die Schule bringen zu können.
Krankheitsbedingt gab es leider Ausfälle in der Durchführung der Projektarbeiten in der Schule in den letzten Werkstunden des Jahres.
Die Grundierung und Nachlackierung der reparierten Stellen und einiger Rohre am Rumpfgestell ist inzwischen abgeschlossen worden. Der Transport zur Schule wird im nächsten Jahr erfolgen.
Das Projekt im Jahr 2017
Das Neue Jahr hat sehr gut begonnen: Die das Projekt betreuende Freie Waldorfschule hat ihr Konto für Spenden zum Projekt zur Verfügung gestellt. Damit ist für die Fortführung des Projektes der Zugang von Spenden nun wieder sichergestellt.
Freie Waldorfschule Braunschweig
- GLS-Bank
- IBAN DE39 4306 0967 0015 9927 00
- BIC GENODEM1GLS
Alle Spenden bitte mit der Zweckbestimmung “Bergfalke” versehen.
Herrn Büttner und Herrn Kropp sei für diese pragmatische Lösung sehr gedankt.
In der Luftfahrtzeitschrift AEROKURIER wurde ein Artikel über unser Projekt geschrieben. Wir danken der Redaktion für diesen Bericht. Der Bericht ist nachzulesen unter :
9. Januar 2017
- Das fertig lackierte Rumpfgestell wurde aus der Werkstatt des Aeroclubs wieder in die Waldorfschule geholt.
- Das im alten Jahr noch nicht vollzogene Verleimen von gebauten Endrippen zu Flügelsegmenten wurde abgeschlossen. Wir werden daran das Bespannen mit Stoff und Folie üben können.
- Da die ganze Fußpedalsteuerung nicht mehr vorhanden ist, wurden nach Konstruktionszeichnungen des Flugzeuges Vorrichtungen gebaut, um die für den Neubau notwendigen Stahlrohre zu positionieren. In diesen Vorrichtungen werden die eingepassten Stahlrohre nur schweißtechnisch geheftet. Das Fertigschweißen übernimmt unser Flugzeugschweißer Carsten.
- Mit dem Einpassen von Stahlrohren in die Vorrichtungen wurde begonnen. Die Stahlrohre haben eine Wandstärke von 0,5 mm.
Eine der gebauten Vorrichtungen zur Positionierung und Anpassung der Rohre für die Pedale.
16. Januar
Das Biegen eines Rohrteiles der vorderen Fußpedalsteuerung für die Seitenruderpedale war das Thema der heutigen Werkstunden. Die zwei 12 mm im Durchmesser mit einer Wandstärke von 0,5 mm Rohre bilden den oberen runden Abschluss der beiden vorderen Seitenruderpedale.
Für das Biegen der Stahlrohre unter Hitze wurde ein feuerfestes Formteil aus Spanplatte, Fermacell und Aluteilen hergestellt.
Eine Seite mit einem soliden Holzkorken verschließen, mit feinem Sand unter Klopfen am Rohr gut verdichtet auffüllen und mit einem weiteren Holzkorken fest verschließen.
Der eingefüllte Sand hält das Rohr beim Biegen in Form.
Mit einem Propangasbrenner wurde das Rohr stückweise glühend erhitzt und dabei um das Formteil aus Alu ziehend gebogen. Hört sich leichter an, als ungeübt getan.
Wir haben geübt und dabei drei Stücke hergestellt…. heiße Sache ….
Das überschüssige Rohr zum Festklemmen und Anfassen beim Verformungsprozess kann noch für die geraden Bauteile weiterverwendet werden.
Das Formteil zum Biegen des Rohres nach der Arbeit.
Eines der Bögen mit bereits grob abgetrenntem Rohrteil und die zugehörige Vorrichtung für den Zusammenbau.
20. Januar 2017
Mit dem Einpassen der Stahlrohre für die Fußsteuerung wurde fortgefahren.
Die Rohre für die Cabriohaube wurden zugeschnitten. Die auf dem Rumpfrahmen liegenden Rohre wurden kalt entsprechend der Kontur gebogen.
Mit dem Einpassen der ersten Rohre wurde begonnen.
23. Januar 2017
Das Einpassen der Stahlrohre für die Fußsteuerung wurde fortgeführt.
Die Formleistenhalter aus Holz wurden am Rumpfgestell festgebunden. Die seitlichen Formleisten selber werden aber noch nicht fertig montiert. Ebenso werden die Metalladapter zur Befestigung der Leisten erst mit der finalen Montage dieser Formleisten festgeklebt. Die Gefahr der Beschädigung der Formleisten und der Adapter wird bei den weiteren Arbeiten am Rumpf, als zu groß erachtet, da diese Elemente aus dem Gestell herausragen. Diese Endmontage geschieht erst nach dem kompletten Einbau der Steuerung.
Die seitlichen Formleisten am Rumpfgestell.
Die festgebundenen Abstandshalter aus Holzleisten mit den Adaptern zur Befestigung der Formleisten.
27. Januar :
Das Einpassen der Stahlrohre für die Fußsteuerung wurde weitergeführt und dabei gelernt, dass diese Metallarbeit ein feinfühliges Arbeiten und eine Vorstellungskraft von den Rohrverschneidungen erfordert. Ebenso wurde hier die geschickte Handhabung einer Rundfeile geübt. Die Rundfeile hat nicht den Durchmesser der benötigten größeren Ausrundungen in den 0,5 mm starken Rohren.
Die provisorisch zur Ausrichtung der Distanzstäbe angebrachten Formholzleisten bekamen nochmal einen letzten Lackauftrag.
Das Einpassen der Rohre für die Cabrioverkleidung wurde auch fortgeführt.
In den nächsten 4 Wochen bis zum 24. Februar findet mit den Schülern kein Werkuntericht statt, da ein mehrwöchiges Praktikum ansteht.
Die Arbeit geht aber dennoch weiter und darüber wird auch berichtet.
Wir haben von der Firma Messer Cutting Systems GmbH das so heiß gewünschte Schweißgeräte MINITHERM HA gespendet bekommen.
Das war eine Nachlieferung vom Weihnachtsmann … :-)))
DANKE
Das Schweißgerät wird in den nächsten Wochen auch zum Einsatz kommen.
Der Koffer mit dem leichten Schweißgerät MINITHERM HA.
Wir danken sehr für die Beachtung und Unterstützung unseres Schulprojektes.
———————————————————-
3. Februar :
Die Rohrstücke für die Fußpedale der Seitenrudersteuerung sind alle angepasst und werden im WIG-Verfahren geheftet und dann autogen fertig geschweißt. Das Heften mit der Flamme würde die Holzhaltevorrichtung anbrennen und dann stinkt es …. will keiner …
Die Pedale für vorne (rechts) und hinten sind fertig zum Heften und Schweißen in den Haltevorrichtungen fixiert. An den hinteren Pedalen (links) werden nach dem Schweißen noch die Befestigungslaschen unten angepasst. Das sind zwei Bleche mit Loch. Weitere Bleche und Rohre für die Steuerseilanbindung folgen, nachdem die Pedalgrundstruktur ein solides Gebilde geworden ist. Für die passgenaue Ausrichtung sorgen dann andere Haltevorrichtungen. Wir könnten in die Serienfertigung gehen … :-))
5. Februar :
Die Fixierungsvorrichtung mit den angepassten Teilen für die zentrale Lagerung der vorderen Seitenruderpedale. Das ist eine Schwinge, an der an dem kleinen Querrohr links und rechts, auf einem durchgesteckten Rohr hoher Festigkeit, die Pedale kippbar befestigt sind.
Die noch notwendigen Blechteile werden von Schülern in der Heinrich-Büssing Berufsschule hergestellt. Dort wird auch die Fallschirmwanne des vorderen Sitzes sowie die Radverkleidung neu gebaut.
13. Februar :
Die nebenstehende Helling dient der Erweiterung der vorderen Fußpedale um die Rohrkonstruktion zur Aufnahme der Anlenkpunkte für die Steuerseile des Seitenruders.
Eine sehr gute Nachricht hat uns erreicht.
Die Braunschweiger Firma Streiff & Helmold unterstützt uns mit 15 mm starken Wellpappenplatten zum Bau von Aufbewahrungskartons für die Leitwerke und die Querruder.
Wir danken sehr für die Anerkennung unseres Schulprojektes und für die Spende.
Der Bau der Kartons wird von den Schülern durchgeführt. Wenn die Kartons fertig sind, können darin die Leitwerksteile und die Querruder zur Schule gebracht werden. Nach einer Übungsphase an einfachen Rahmenbauteilen und den vorher gebauten Flügelsektionen werden dann diese kleineren Flugzeugteile mit Hilfe der Schüler mit Stoff bespannt.
Das Aufbringen des Spannlackes kann aber wegen eventueller Gesundheitsgefahren nicht mit den Schülern gemacht werden.
17. Februar :
Die Pappen sind während einer regenfreie Wetterlücke bei der Fa. Streiff Helmold abgeholt worden und belagern jetzt den Werkraum in der Schule. Die 2,4 x 2,4 m Pappen mussten einseitig auf ein reduziertes Maß geschnitten werden, damit sie auf den Dachgepäckträger passten. Danke an den netten Mitarbeiter, der mir geholfen hat.
Am Montag steigen wir in die Pappkartonfabrikation ein…. 🙂
20. Februar :
Die Fertigung der Transport-. und Schutzkartons aus der gespendeten Wellpappe hat begonnen.
Zwei Sorten Wellpappe stehen zur Verfügung : 15 mm für die Seitenwände und 7 mm in geknickter Form für die Eckaussteifungen.
Die 15 mm Platten werden nach dem Zuschnitt an den Kanten eingeschlitzt und dann zum Karton geknickt.
Die Ecken werden mit der 7 mm Pappe oder mit soliden Pappwinkeln verstärkt.
Der fertige Karton für die Aufbewahrung der Störklappen
Bei den 4,5 m langen Kisten für die Querruder fehlt noch der Deckel.
Geklebt wurde mit Heißkleber aus zwei Heißklebepistolen. Die ganzen vorhandenen Klebesticks wurden verflüssigt.
24. Februar:
Der Kartonbau ging weiter. Notwendiger Nachschub an Klebesticks wurde beschafft. Der Karton für die Seitenleitwerksfinne ist fertig. Ebenso sind die zwei großen 4,8 m langen Kartons für die Querruder fertig und werden in den nächsten regenfreien Tagen zum Aeroclub gebracht um dort die Queruder aufnehmen zu können. Es fehlen noch die Kartons für das Höhenleitwerk und die Fertigstellung des Kartons für das Seitenruder.
Bei der Arbeit … Der Einsatz von zwei Heißklebepistolen und notwendige Schnelligkeit ist angesagt, damit der Heißkleber ordentlich klebt.
Die Anlenkpunkte der Fußsteuerung wurde am Rumpfgerüst vermessen und festgestellt, dass hier angepasste Ausführungen für die linke und die rechte Seite der Pedale hergestellt werden müssen…. normal für einen Bergfalken … :-))
25. Februar:
Die 4,8 m langen Kartons für die Querruder konnten bei gutem Wetter zum Braunschweiger Aeroclub gebracht werden.
Die Queruder passen in die Kartons …. Es ist schön, wenn ein Plan funktioniert …. :-). Rechts die eingelagerten Flügel des Bergfalken.
Einige kreativ tätige Lehrkräfte der Waldorfschule haben reges Interesse und Begehrlichkeit an den großen 15 mm dicken Wellkartonplatten geäußert, super Material für den Kulissenbau … In zwei Wochen am 10./11. März finden Theaterspiele der Klasse 8 statt und die Mädchen und Jungs sind mit den Lehrkräften derzeit sehr fleißig mit dem Kulissenbau beschäftigt.
Da wir zuviel Kartonplatten haben, konnten Pappen zur Verfügung gestellt werden und ganz fix entstanden Kulissen.
27. Februar:
Zwei restliche Kartons fertigen und einen begonnenen Karton mit Deckel komplettieren … mal schaun wie weit wir kommen…….. Das Tolle an der Arbeit ist, dass man sieht, was geschaffen wurde : raumgreifende Objekte.
Direkt am Flugzeug wurde auch was bewegt:
Letztens wurde ja festgestellt, dass die Anlenkpunkte der hinteren Fußsteuerung für die linke und für die rechte Seite der Pedale unterschiedliche Abmaße haben.
Die an die Pedale anzuschweißenden Laschenteile wurde mit einer einfachen Vorrichtung auf das jeweilig passende Maß fixiert und werden mit dieser Vorrichtung dann eingepasst und angeschweißt.
06. März:
Weiterbau der Kartons …
Probeeinbau der Schlepp-Kupplungen. Die anderen Steuerungsteile werden demnächst erstmal probeweise eingebaut und die Länge der notwendigen neuen Schrauben bestimmt.
Anbringen einer Kartonauflage für die Querruderkisten, die so bald als möglich bei regenfreiem Wetter mit den Querrudern in die Schule transportiert werden.
Nach dem Üben des Bespannens werden die Querruder bespannt.
9. März
Heute Morgen war regenfreies Wetter und damit ein passender Zeitpunkt für den Transport der Pappkisten mit den Querrudern vom Aeroclub im Weinbergweg zur Waldorfschule.
Eine sehr angenehme Überraschung erfuhr ich dann in der Schule. Ohne fragen zu müssen, boten gleich mehrere Schüler Hilfe beim Entladen an. Im Hintergrund liegen die Queruderkisten schon auf dem Schrank und der neuen Ablage. Die Schüler räumen gerade die anderen noch in Arbeit befindlichen Kisten wieder in die Ecke.
— Die Kisten sind sehr leicht … das ist nur Show was da gemacht wird 🙂 —
Leider ist das Bild ein miserables Produkt meines Mobiltelefons, aber es soll hier trotzdem veröffentlicht werden. Ich bin immer wieder begeistert und sehr erfreut, wenn spontan Hilfe angeboten wird. Herzlichen Dank an die Schüler … 🙂
10. März:
Da das Werken am Freitag nicht mehr im Schulplan steht, ist dies ein Sondertag … : Julian biete an, „außerschulisch“ weiterzumachen, da er frei hat. Das wird mit Dank gerne angenommen … 🙂
Die geplante Fertigstellung der Pappkartons wurde erledigt und sogar noch mehr: Die vier Störklappen des Flügels wurden in ihre Einzelteile zerlegt.
Leider gab es dann ein AHA- Erlebniss, als ein Höhenruderteil in den Karton gelegt wurde.
Dumm gelaufen …… Der „Meister“ hat Schuld, er hat falsche Maße vorgegeben … drum durfte er die Kartons auch wieder zur Schule bringen. Am Montag gibt es somit einen bisher nicht eingeplanten weiteren Arbeitspunkt.
Mit der Fehlbarkeit bin ich aber in sehr guter Gesellschaft : Der Pabst soll jüngst gesagt haben: „.. auch ich bin nur ein fehlbarer Sünder“.
13. März:
Die beiden zu kurzen Kartonkisten wurden von Rico verlängert. Im Hintergrund auf dem Gestell die Kisten für die Querruder mit einem Querruder davor. Diese Position wird uns auch dienlich sein, wenn die Querruder nach dem Kleblackauftrag trocknen müssen.
Der „Trockeneinbau“ der Steuerung wurde von Julian begonnen. „Trockeneinbau“ bedeutet, dass alle Steuerungsteile erstmal probeweise mit einfachen Schrauben zusammengesetzt werden, um zu sehen wie alles passt und welche Verbindungsbolzen oder Schrauben eventuell neu benötigt werden. Aufgetragener Lack in Lagerungen wird dabei entfernt. Zusammengebaut wurde das Bremsklappengestänge und die Lagerungen für die Höhenruderstange. Das vorliegende Bild wurde erst gemacht, als der Rumpf schon wieder in der Wandposition hing und zeigt nur einen Teil der Arbeit.
Auf den drei Übungsrippensektionen wurde Klebelack an der Auflagefläche zur Bespannung mehrfach (7x) aufgebracht. Ein langwieriger Prozess bis sich eine Klebelackschicht entwickelt hat, die nach dem Trocknen noch glänzend ist und eine gewisse Dicke erreicht hat. An diesen Teilen werden wir das Bespannen demnächst üben. Wenn wir das können, kommen die Queruder dran.
15. März:
Die letzten Kartons wurden zum Braunschweiger Aeroclub gebracht und die
beiden Teile des Höhenleitwerks konnten nun „passend“ gelagert werden. Die Seitenruderteile sind in den Kisten im Hintergrund verstaut.
20. März:
Das Bespannen wurde an den gefertigten Flügelsektionen geübt. Nach mehrmaligem Aufstreichens von speziellem Klebelack wurde das Gewebe aufgelegt und mit einem Spezialverdünner durch das Gewebe wieder angelöst und dadurch durch das Gewebe gedrückt. Wenn es „glitschig“ auf der Oberseite des Gewebes wird, ist es gelungen. Wichtig ist die komplette Umschließung der Gewebefasern mit dem Klebelack.
Noch ist die Bespannung wellig ….
Nach dem sicheren Aushärtens des Klebelackes wird das Gewebe durch Wärmeeintrag mit einem Bügeleisen oder Fön gestrafft. …. Das passiert in der nächsten Woche…
- Auf einem Querruder wurde auch partiell Klebelack aufgetragen. Da machen wird nächstes Mal wieder eine Bespannübung. Wenn das alles dann gut klappt, werden die Querruder bespannt.
- Für die Bugverkleidung wurde mit der Anfertigung von Zuschnittzeichnungen begonnen.
- Viele kleine Holzteile der Störklappen wurde überarbeitet.
- Der Probe-Einbau der Steuerungsteile in den Rumpf wurde fortgeführt.
27. März:
Die letzte Woche bespannten Bauteile wurden heute mit Wärme behandelt.
Mit Bügeleisen und / oder Heissluftföhn lässt sich das Gewebe straff spannen.
Eine einfache Sache, wenn die Temperatur stimmt. Je höher die Temperatur, umso straffer. Mit einem Thermometer haben wir die Temperatur gemessen. Um die 140 Grad ist brauchbar und gibt eine gute Spannung im Gewebe.
Die Grenze der Stoffbelastung haben wir natürlich ausprobiert. Ab 180 Grad wird es kritisch und bei 200 Grad schmilzt das Gewebe.
Die Rohrrahmen der Störklappen müssen noch von Lack und vor allem von alten Klebematerialien gesäubert werden. Da wurde mal mit Mikroballon versetztem Epoxydharz die alte Sperrholzabdeckung verklebt/repariert. Dort wo mit dem Harz gearbeitet wurde, war die Holzanbindung extrem gut. Wir werden das Harz nun unter Hitzeeinwirkung (~140 Grad) weich machen und abschaben. Die Rohrrahmen werden komplett vom Lack befreit und lacktechnisch neu aufgebaut.
Mit den 4 Störklappenrahmen werden die letzten Teile des Fliegers entlackt und neu aufbereitet.
Ansonsten wurden noch Holzteile zum Einbau in die Störklappen und zum Verkleben mit der Abdeckung gefertigt und die notwendigen Schrauben- oder Bolzenlängen für Teile der Steuerung vermessen.
An einem originalen Querruder wurde auch eine Klebeprobe gemacht. Das hat auch alles gut geklappt, sodass eigentlich die Ruder zur Bespannung fertig wären, wurde so gedacht …… Beim genauerem Hinsehen wurden dann aber festgestellt, dass das vor „Jahrzehnten“ schon aufbereitete Bauteil leider viele in der Lackschickt vorhandene Störkörper hat und ebenso viele Lacknasen eine saubere Bespannung verhindern würden. Also gilt es die Störstellen zu schleifen und wo Metall durchscheint, wieder Lack aufbringen. Mal schaun, ob diese Schnellmaßnahme gut war und wie das nach dem Trocknen aussieht.
3. April:
Die Aktualisierung hat leider länger gedauert als geplant. Durch den Aufenthalt auf der Messe AERO 2017 ab dem 4. 4. und durch nachfolgende familiären Umstände geht es erst jetzt weiter mit der der Aufarbeitung des 3. Aprils und der weiteren Berichterstattung.
Die geplanten Bespannarbeiten an den Querrudern wurden auf später verschoben. Der Grund liegt in der doch notwendigen intensiveren lacktechnischen Überarbeitung der Querruder. Die Oberfläche ist, wie schon beschrieben, auch nach der Schnellmaßnahme noch zu schlecht. Da ist mehr Sorgfalt auszuüben, was Zeit kosten wird.
Ebenso gab es zwei Stellen pro Querruder, wo die Verklebung für eine ordentliche Bespannung reichlich unklar war, bzw. dafür kein Klebeuntergrund vorhanden war.
Da haben wir nachgebessert.
Das Anbringen der Bespannung an den Antriebshebel ist nicht möglich, da der Hebel senkrecht in das bespannte Querruder geht.
Als Klebeauflage für die Bespannung wurde ein Sperrholzkragen um den Antriebshebel geklebt. An einer anderen Stelle wurde eine weitere sinnvolle Vergrößerung der Klebefläche eingebaut.
Der Einbau der Steuerungsteile wurde fortgeführt. Bei den neu ausgebuchsten Lagerungen der Bremsklappenhebel mussten wir feststellen, dass die neuen vorgesehenen Schrauben wegen geringfügigem Übermaß nicht montiert werden konnten. Dort muss nun mit einer Reibahle nachgearbeitet werden.
Die Osterferien sind am 24. April vorüber und es geht in den Endspurt des Schuljahres.
Plan für den 24. April:
Von den Rohren der Störklappen wurden der Lack entfernt. Der provisorische Steuerungseinbau wurde abgeschlossen und für den endgültigen Einbau die jetzt notwendigen Schrauben und Bolzen definiert. Das Sperrholz für die Störklappen wurde zugeschnitten und für den späteren Anbau vorbereitet. Dazu gehören auch die Holzteile, die in den Rohrrahmen der Störklappen den sicheren Halt der Beplankung geben.
Einbau der Bugkupplung
Wir hatten auch Besuch von einer Redakteurin der Braunschweiger Zeitung. Der Artikel erschien bereits am 26. April.
Der folgende Werkunterrichtstag war der 1. Mai, was zum Ausfall der Arbeiten führte.
Plan für den 8. Mai:
- kleiner Lehruntericht mit Kreide und Tafel zu dem Thema Strömungen in der Umwelt. Das Strömen von Wasser und Luft um Hindernisse und deren Auswirkung soll betrachtet werden. Warum ein Flugzeug fliegen kann soll zum Schluss verstanden werden.
Das war geplant und ein sehr praxis orientierter umfangreicher Unterrichtsstoff mit vielen Expermentalmodelle wurde vorbereitet ….. aber wie es manchmal so kommt im Leben, gibt es plötzlich Änderungen.
So wurde dann leider um 10 Uhr in Erfahrung gebracht, dass der heutige Vormittag von den Lehrern für andere Aktivitäten eingeplant wurde und der Werkunterricht und damit unser Strömungsunterricht ausfällt. ……….. Schade ………..
Da der 8.Mai aber die letzte Unterichtseinheit im Werken vor den Sommerferien war, hieß es, von den Schülern Abschied zu nehmen. Die Schüler beenden in diesem Jahr ihre Schulausbildung an der Waldorfschule und gehen in die Lehre bzw. auf weiterführende Schulen.
Ich wünsche den beiden bis zum Schluss gut an dem Projekt mitgemachten Schülern Julian und Rico, für Ihren weiteren Lebensweg viel Glück und die schon im Projekt gezeigte Kraft zum Durchhalten im Leben, zu bewahren. Ebenso sei den anderen Schülern, die kurzzeitig im Projekt mit dabei waren, für Ihren Einsatz gedankt und ebenso gute Zeiten in Ihrem Leben gewünscht.
Eine Klassenfahrt und andere Aktivitäten in der Schule füllten die restliche Zeit des Schuljahres aus.
_____________________________________________________
_________________________________
_______________
______
_
Das Schuljahr 2017 – 2018
Mit Arne und Marvin wird in ihrem 12 Schuljahresgang die Restaurierung fortgeführt.
Herzlich Willkommen im Projekt … :-))
Arne
Marvin
Jeden Freitag wird von 10 Uhr bis 12:30 Uhr gearbeitet.
18.08.2017:
Mit der Fertigstellung von Arbeiten an den Querrudern, die bis zum Bespannen mit Stoff gehen werden, werden die Arbeiten fortgeführt.
Die Lackoberfläche der Rohrkonstruktion der Querruder hat leider noch nicht die Güte, um eine saubere Bespannung durchführen zu können. Die Oberfläche muss frei von in der Farbe enthaltenen Schmutzpartikeln sein. Das war bisher noch nicht der Fall.
Ebenso wird die Struktur der Querruders um kleine zusätzliche Sperrholzfahnen in den Bereichen der Ruderbefestigung ergänzt. Wir haben damit im letzten Schuljahr schon mal bei den Ruderantrieben angefangen. Diese zusätzlichen an das Rohrgerüst angeklebten Sperrholzfahnen geben eine vergrößerte Klebefläche für die Bespannung.
Marvin beim Schleifen der Rohrkonstruktion eines Querruders
Nach dem Glätten der Oberfläche und dem zusätzlichen Einbau der Sperrholzfahnen wird das Bauteil mit einer Spritzpistole pickelfrei lackiert.
Es werden in den folgenden Werkstunden konzentriert die Querruder bearbeitet und final bespannt. Die Queruder werden anschließend in den gefertigten Kartonkisten bis zum Lackieren des ganzen Flugzeuges gelagert.
01.09.2017:
Heute waren wir zu zweit, da Marvin krank ist … gute Besserung.
Arne hat alle Sperrholzfahnen fertiggestellt. Mit Araldit 2014 wurden die Teile an die Querruderrohre geklebt. Ein leichtes Spachteln und Glattschleifen wird noch folgen.
Das Sperrholz vergrößert die sichere Verklebung der Bespannung im Bereich der Lagerungen
Dieses Teil wurde schon mit dem letzten Schuljahrgang hergestellt und verklebt und ist nun fertig gespachelt und verschliffen.
Die Klebungen können nun bis Sonntag aushärten. Am Sonntag wurde noch Spachtel auf die Übergangsbereiche der Holzfahnen aufgebracht und die Querruder auf höhere Ablagen gelegt, damit am Montag der Werkraum den anderen Schülern wieder zur Verfügung steht.
Die restliche Zeit wurde mit Schleifarbeiten am Haubenrahmen verbracht. Mit solchen kleinen Lückenfüllertätigkeiten wird das Teil auch mal fertig zum Lackieren.
08.09.2017:
Heute waren wir leider wieder nur zu zweit. Marvin war zwar inzwischen genesen, hat sich dann aber leider beim Sport ein Verletzung zugezogen …. Gute Besserung … werde bald wieder gesund und fit, wir brauchen dich !
Weiter ging es mit den Querrudern. In der vergangenen Woche war leider außerhalb des Werkunterrichtes keine Zeit, die Lackarbeiten weiterzuführen.
So wurden heute die Spachtelungen des letzten Sonntags verschliffen und nochmal gründlich die Oberflächen der beiden Querrudergerippe bearbeitet und anschließend sorgfältig vom Staub gereinigt.
Auf die bis auf das Metall durchgeschliffenen Lackstellen wurden mit einer Spritzpistole Primer aufgetragen und gleich mit einem Heißluftföhn getrocknet, damit beide Seiten unmittelbar lackiert werden konnten.
Draussen vor der Tür wurde der Endlack aufgetragen.
etwas später eine kurze Zwischenlagerung zum Antrocknen in der Werkstatt.
und dann vorsichtig auf den Regalen in der Höhe gelagert. Hier kann der Lack nun gut durchhärten und die Querruder stören nicht mehr in der Werkstatt.
Wir haben sehr viel geschafft. In der nächsten Werkstunde kann mit den Vorbereitungen für das Bespannen begonnen werden.
15.09.2017
Wie geplant, wurden heute die beiden Querruder mit Klebelack von Fa. IRSA eingestrichen.
5 Anstriche waren notwendig, bis eine genügend dicke Schicht zur Weiterverarbeitung aufgetragen war. 1 ganze Dose wurde verbraucht ……. 😦 Das war der Rest, den wir hatten.
Das Wetter war gut und wir konnten draussen die Arbeit machen. Der Geruch des Klebelacks hätte sonst als Droge gewirkt ….
Manfred kam auch vorbei und machte gleich mit …
29.09.2017:
Es ging wie geplant weiter. Das Wetter war gut und wir konnten draussen arbeiten.
Hier wird keine Kaffeetafel gedeckt, sondern auf zwei Tapeziertischen das Gewebe für die beiden Querruder zugeschnitten.
Vor dem Aufbringen des Gewebes wird nochmals ein Klebelackanstrich vorgenommen. Der von Fa. IRSA gespendete Klebelack kam rechtzeitig.
Einen großen Dank an Frau Sallinger von Fa. IRSA für die Empathie zu diesem Projekt und der Zusage für weitere Unterstützungen.
Begonnen wurde in der Querrudermitte. Mit Spezialverdünnung wird durch das Gewebe der Klebelack unter dem Gewebe angelöst und dann durch den Stoff massiert. Wichtig ist, dass die Fasern des Polyestergewebes ganz vom Klebelack umschlossen sind. Wo es nicht ganz aussreicht und keine klitschige Oberfläche entsteht, wird von oben Klebelack nachgereicht. Beulen und Falten im Gewebe werden später durch das Erhitzen mit einem Bügeleisen ähnlichem Gerät straffgespannt. Das Gewebe schrumpft bei Wärmeeintrag.
Hier ist schon die andere Seite zu sehen, die mit dem Gewebe bedeckt wurde. Die Arbeit ging leicht von der Hand. Allerdings wurde uns durch die Lösungsmitteldämpfe leicht „dusselig“, trotz der Arbeit im Freien. Da wir zukünftig die weiteren Arbeiten wohl wegen der Witterung in einem geschlossenen Raum machen müssen, ist hier dringend Hilfe in Form von Atemschutzmasken mit den entsprechenden Filtern notwendig. Selbst bei der Arbeit im Freien sollten diese getragen werden da die Nase doch zu dicht am Objekt ist.
Das fertig bespannte Querruder. Kleine Nacharbeiten am Randbogen sind noch nötig. Wir sind innerhalb der 2,5 Stunden gut fertig geworden und werden somit nach den hier in Niedersachsen stattfindenden Herbstferien in der folgenden Werkzeit am Freitag das andere Querruder bespannen.
HERBSTFERIEN
Am 10. Oktober hat uns Herr Woltersdorf von der Firma Swix-Sport GmbH besucht und das zugesagte Heizgerät übergeben. Herrn Woltersdorf wurden in der Waldorfschule die in Arbeit befindlichen Baugruppen direkt vor Ort vorgestellt. Er war sehr beeindruckt von der in Angriff genommenen umfangreichen Arbeit und wünscht dem Projekt ein gutes weiteres Gelingen.
Wir danken ganz herzlich für diese Spende, die uns bei den Bespannarbeiten wertvolle Dienst leisten wird.
Dieses zum professionellen Waxen von Skier entwickelte Gerät ist für das Schrumpfen des Polyestergewebes sehr gut einsetzbar. Dieses Gerät vom Typ T18 zeichnet sich durch eine sehr stabile Temperaturregelung aus.
Hier wurde es gleich an einem Teststück ausprobiert. Die Temperatur wird perfekt konstant eingehalten.
Am 13. Oktober erreichte uns eine sehr erfreuliche Nachricht von der Vertretung der Firma Linde.
Für den Zeitraum von 2 Jahren erhalten wir kostenfrei zwei Gasflaschen mit Azetylen und Sauerstoff zur Verfügung gestellt.
Die Ausbildung eines Flugzeugschweißers und die Fertgstellung der fehlenden Steuerungsteile sowie der Cabriohaube ist damit sichergestellt.
Vielen herzlichen Dank für die Hilfe!
20.10.2017:
Das weitere Bespannen der Querruder wird erstmal zurückgestellt bis Atemschutzmasken vorhanden sind. Wir hoffen noch auf eine Spende dieser Masken. Sonst müssen wir das derzeit wenige Geld dafür ausgeben.
Alternativ ging es wie geplant mit der Anfertigung von Schablonen für die vordere Rumpfverkleidung weiter.
Herrn Hilker sei herzlich für die Spende von nutzbaren Pappen gedankt, die er aus seinem Betrieb freundlicherweise zur Verfügung gestellt hat.
Die Rumpfverkleidung wird aus aufgeklebten Sperrholzplatten sowie im Bereich für die Wartungsarbeiten im Rumpfnasenbereich aus anschraubbaren Aluminiumblechen hergestellt.
Das Rumpfgerüst liegt auf der Seite und eine Schablone wird für ein aus Alublech zu fertigendes Verkleidungsteil angepasst.
Mit Hilfe der Schablonen werden am nächsten Freitag die Verkleidungsteile aus den Sperrholzplatten herausgeschnitten und bereits auf dem Rumpfgerüst verklebt.
Ein verwackeltes Bild der Schablonen aus Pappe.
Der Arbeitsgang der Fertigung der Verkleidungsteile sowie das Aufkleben auf den Rumpf wird bis zur Fertigstellung fortgeführt.
Der Umbau der Haubenhelling sowie das Fortführen der Bespannarbeiten an den Querrudern erfolgt später.
27.10.2017:
Es ging nach Plan weiter:
Mit Hilfe der Schablonen wurden die Verkleidungsteile auf die Sperrholzplatte aufgezeichnet und mit einer Schwingsäge ausgeschnitten.
Das Rumpfgerüst liegt auf der rechten Seite und die obere linke Verkleidung wurde mit Araldite 2014 aufgeklebt und mit Tape festgehalten.
Die beiden oberen seitlichen Verkleidungsteile sind aufgeklebt. Nächstes Mal wird die obere Verkleidung und ein vorderes Seitenteil angeklebt. Die anderen Verkleidungsteile bestehen aus Blech und werden mit dem Rumpf verschraubt. Durch diese abnehmbaren Verkleidungen kann die Wartung an Bugkupplung und Steuerungseinbauten vorgenommen werden.
Das schräg herausstehende Holzteil ist eine schnelle Hilfsvorrichtung, um zwischen der Beplankung und dieser Hilfsvorrichtung eine Stützung anzubringen. Die Beplankung hatte eine Beule geworfen und die wurde damit weggedrückt damit die Verklebung am Rand nicht diese Beule noch fixiert.
Nächstes Mal wissen wir mehr, ob diese Beulneigung geblieben ist. Sonst werden andere Maßnahmen ergriffen. Eine Beule wird es nicht geben !
03.11.2017:
Es ging weiter nach Plan. Die befürchteten Beulen gab es nicht, dafür hatte an einer Stelle das Klebeband zur Fixierung versagt und das Sperrholz war nicht am Rohr angeklebt. Diese Fehlstelle wurde von den Kleberresten ausgeputzt und neu verklebt.
Die beiden noch fehlenden Verkleidungsteile wurden nach Schablone ausgesägt.
Nach dem Verputzen der Ränder von den bereits aufgeklebten Holzplatten, konnten die anderen Platten aufgeklebt werden. Mit Hilfe von Packtape und anderen Klebebändern wurden diese Teile gut festgezogen.
Die noch fehlenden Verkleidungsteile werden aus Aluminiumblech hergestellt.
Nebenbei wurde an dem Haubengestell geschliffen. Diese Zwischenarbeiten wird es immer geben, um die 2,5 Std. Zeit gut auszunutzen.
10.11.2017
Leider waren wir heute insgesamt nur zu zweit.
Die verklebten Holzteile der Rumpfnasenverkleidung wurden an den Nahtstellen verschliffen.
Das sieht schon schön aus. Die senkrechte Wand wurde heute noch mit angedickten zund mit Fasern versetztem Epoyharz mit der dahinter befindlichen Strebe verklebt. Zwischen der Wand und der Strebe musste ein 3 mm Spalt gefüllt werden, sonst hätte es eine Beule gegeben. Beulen wollen wir nicht 🙂
Ein stets schönes Gefühl, über geschliffenes Holz zu streichen. Die noch fehlenden Verkleidungsteile aus Blech sind in der Berufsschule „in Auftrag“ gegeben worden.
Um die Feuerfestigkeit der Helling zum Bau der Cabriohaube zu bekommen, sägt Arne die notwendigen Stücke aus Fermacell-Platten heraus. Auf der Helling werden die Rohre autogen, d.h. mit der Schweißflamme, geheftet und dann abseits der Helling verschweißt.
Mit den Stützhölzern, die , hoffen wir mal 🙂 , ruhig aus Holz sein können ist die Helling nun fertig für die anstehenden Heft- und Schweißarbeiten des Cabriohaubenrahmens. Zur Duchführung der Schweißarbeiten wird die Helling in die Metallwerkstatt gebracht ……. das nächste Mal.
Die Zeit war wieder schnell um und die oben angesprochene Verklebung der Seitenwand wurde in der Wandablageposition des Rumpfes von einer Leiter aus gemacht. Da Arne noch andere geplante Aktivitäten in der Schule zu erledigen hatte, musste vorher der Rumpf wieder den Arbeitsbereich der Werkstatt frei machen.
17.11.2017:
Wir haben heute die Arbeit an der Bespannung fortgeführt, die vor Wochen schon mal an einen Querruder gemacht wurde. Damal waren wir nicht ganz fertig geworden.
Das auf den Holm auslaufende Gewebe wurde erneut mit Verdünnung getränkt und mit Zugabe von Klebelack jetzt festanliegend verklebt.
An dem gebogen auslaufenden Rand des äußeren Querruderendes wurden das überlappende Gewebe verklebt. Das ging mal einfacher als gedacht.
Bei dem nächsten Querruder werden wir in den 2,5 Std. nur eine Seite bespannen und die aber komplett fertig machen.
An der Helling wurden noch kleine Arbeiten bezüglich der Festlegung der Rohre getätigt.
Die zwei großen Seitenverkleidungen aus Holz vom Rumpfcockpit wurden mit der Schwingsäge ausgeschnitten und können dann, wenn die Seitenformleisten angebracht sind, aufgeklebt werden. Zum Anpassen der Blechverkleidungen muss der Rumpf auf die Seite gelegt werden und da stören die Formleisten derzeit noch.
24.11.2017:
Heute haben wir die Unterseite des 2. Querruders bespannt. Zuvor wurden noch zwei Lagen Klebelack frisch aufgetragen und mit einem Fön abgelüftet. Mit lösemittelfesten Handschuhen und den Atemschutzmasken ging das sehr gut. Die Werkstatt stank schon recht stark und es kamen auch erste Klagen von Mitarbeitern der Waldorfschule, weil wohl der Werkraum am letzten Wochenende noch deutlich nach dem Lösungsmittel roch. Wir hatten zwar gelüftet, aber wohl zu wenig. Wir ahnten nicht, dass am Wochenende dort gearbeitet wurde…. 😦 Heute wurde die Tür nach unserem Arbeitsschluss auf gelassen und musste dann später von Mitarbeitern geschlossen werden.
Das Bespannen der Unterseite gelang uns sehr gut. Die restliche Arbeitszeit reichte für das Bespannen der anderen Seite nicht mehr. Das war aber auch so geplant. Die Arbeit ohne Zeitdruck auszuführen war gut. Leider ist nur noch Arne beim Projekt dabei. Dafür leistet er aber perfekte Arbeit.
Nach dem Bespannen hatten wir noch Zeit und nahmen uns das erste schon komplett bespannte Querruder vor. Mit dem von Fa. TAKO gespendeten Bügeleisen gelang das Spannen des Gewebes hervorragend.
Das Bügeleisen TAKO-T18 im Einsatz. Sehr spassig zu sehen, wie das Gewebe sich strafft.
Allerdings stellten wir fest, dass an einigen Stellen das Gewebe etwas zu weit um das Holmrohr festgeklebt war, sodass hier eine negative Kante entstand… sehr unschön .. Einige dieser Stellen haben wir mit einem örtlichen Wiederanlösen abheben können. Die „Reparatur“ funktioniert. Wir werden nächstes Mal die anderen mangelhaften Stellen noch nacharbeiten.
Erfahrung zu gewinnen ist eine Sache des Selbermachens und des kritischen Bewertens der eigenen Arbeit … wir lernen !
08.12.2017
Der Plan sah eigentlich vor, dass wir heute das 2. Querruder fertig bespannen wollten.
Daraus wurde aber nichts, weil wir uns erhebliche Klagen von den Lehrkräften der Schule über die Geruchsbelästigung des Lösungsmittels anhören mussten. Nach der Arbeit am Freitag und trotz Lüftens waren wohl am Montag noch immer Reste des Lösungsmittels zu riechen. Zum Schutze der Gesundheit der Jugendlichen und der Lehrkräfte können wir diese Arbeit so nicht weitermachen.
Damit werden weitere Bespannarbeiten an den Rudern, bzw. des Rumpfes mit den am Projekt beteiligten Werkschülern nicht mehr in der Schule durchgeführt werden können. Es ist zu bemerken, dass die bei den Bespannarbeiten Beteiligten mit Atemschutzmasken die Arbeit versehen. Eine Gefährdung der am Projekt arbeitenden Schüler ist damit ausgeschlossen.
Da es für weitere Arbeiten an dem Tag keine andere Planung und Vorarbeit gab, wurde alternativ an der Lackierung der Haube und an dem Zuschneiden von Rohrstücken für die Cabrio-Haube weitergearbeitet.
—————————————-
Erfreulicherweise hat sich noch ein Mitstreiter für die Restaurierung des Bergfalken eingefunden. Rolf Vollrath, pensionierter Lehrer und in jungen Jahren auch Mitglied des Braunschweiger Aeroclubs, hat Gefallen daran gefunden, an der Restaurierung des Flugzeuges, auf dem er das Fliegen gelernt hat, mitzuwirken.
Rolf, herzlich Willkommen im Projekt.
15.12.2017:
Mit Arne und Rolf wurden der letzte Einsatz am Bergfalken in diesem Jahr gemacht.
Die Lackierung des Haubenrahmens wurde fortgeführt.
Die uns von der Heinrich Büssing Berufschule nach Schablone zugeschnittenen Bleche für die Bugverkleidung wurden angebracht.
Dabei stellte sich leider heraus, dass die M5 Gewinde der im Rumpfgerüst eingeschweißten Muttern sehr ausgeleiert waren. Es wurde erstmal auf die nächste Gewindestufe M6 ausgewichen. In der Werkstunde werden M5 Gewinde eingebaut.
Die fertig montierten und abnehmbaren Blechverkleidungen aus 0,5 mm Alublech.
Für die Fußbretter des hinteren Sitzes wurden dünne Sperrholzplatten zugeschnitten und zu einem Sandwich aus Sperrholz und einem Wabenmaterial verpresst. Diese Bodenbretter werden bei gleichem oder weniger Gewicht eine höhere Festigkeit aufweisen als die alten Fußbretter.
Das Projekt im Jahr 2018
Allen Spendern und Lesern und am Projekt Mitwirkenden sei ein gesundes und zufriedenes neues Jahr gewünscht.
Das Projekt wird mit Arne und Rolf fortgeführt. Marvin hat in 2017 die Schule verlassen. Wir danken für seine Mitarbeit und wünschen einen guten Lebensweg.
12.01.2018:
In der letzten Werkstunde des alten Jahres wurden die von der Heinrich-Büssing Berufsschule hergestellten Verkleidungsbleche am Rumpfbug angepasst und verschraubt. Leider waren die Gewindelöcher für die M5 Schrauben in einem schlechten Zustand. Neue M5-Gewinde wurde durch das Aufbohren der alten Muttern und dem Einsetzen von Einnietmuttern geschaffen. Diese Gewindehülsen werden mit Hilfe einer speziellen (Pop)Nietzange in einem vorgesehenen Bereich der Hülse beim Zusammenziehen gestaucht und verklemmen dadurch, ähnlich der Verarbeitung eines Popniets.
In den Ecken befinden sich die eingeschweißten M5-Muttern für die Befestigung der Blechverkleidungen, die nun zur Aufnahme der Einnietmuttern aufgebohrt wurden.
Eine montierte Senk-Einnietmutter, nach dem Aufbohren und Senken des Loches.
Die Fertigung der Bodenbretter wurde fortgeführt.
Das bisher gebaute (linke) Bodenbrett wurde mit seinen Aussparungen fertiggestellt. Es ist leichter als das Original.
Zuschneiden der neuen Platten für das rechte Bodenbrett. Zum Arbeitsende wurden die Teile noch verklebt und gepresst, damit das Brett in der nächsten Woche weiter bearbeitet werden kann.
Die uns vom Oldtimerfliegerfreund Mario Selss gespendete neue Kufe wurde in den vorderen Aufnahmebereich des Rumpfgestells eingepasst.
Die Lackierung des Haubenrahmens wurde fortgeführt.
19.01.2018: Ausfall wegen Krankheit
26.01.2018:
Heute waren wir zu zweit. Der Bau der Bodenbretter für den hinteren Sitz wurde fortgeführt und verschiedene Vorbereitungen für weitere Arbeiten getroffen.
Das am letzten Werktag verklebte und gepresste (Sperrholz-Wabe-Sperrholz) Brett wurde auf Maß besäumt.
Die „Innneneinrichtung“ kommt voran.
Die an der Seite offene Wabenstruktur der Bodenbretter wurde etwas ausgeschliffen und mit Mikroballoon versetztem Epoxyharz ausgefüllt.
Das Sperrholz für das mittlere Brett des hinteren Sitzes wurde für die Sperrholz-Wabe-Sperrholz Bauweise ausgeschnitten, verklebt und verpresst.
Vorbereitungen für den Bau des vorderen und des hinteren Sitzes wurden gemacht. Es sollen leichtere und stabilere Sitze in entstehen. Auch wird der Sperrholz-Waben Sandwich zum Einsatz kommen.
Unterricht am 16. März 2018
Es wurden die Eigenschaften der Luft und deren Auswirkungen bei der Umströmungen um Objekte des Alltags und von Flugzeugen mit Modellen und Kreide an der Tafel gezeigt und diskutiert.
Die durchgenommenen Themen :
- Die Auswirkungen und das Nutzen der spezifischen Gewichtsunterschiede von Luft, Wasserstoff und Helium beim Betrieb von Ballonen und Luftschiffen.
- Die Möglichkeiten der Kurssteuerung beim Fahren von Ballonen.
- das unterschiedliche Empfinden von Wind vor, zwischen und hinter Gebäuden.
- Das Umströmen von Steinen im Wasser. Der Aufenthaltsort von Fischen.
- Die Neerströmung an Flüssen.
- Das lange Fliegen ohne Flügelschlag der Möven an Schiffen und der Albatrosse über den Wellen.
- Der Hang- und Wellenflug von Segelflugzeugen.
- Das Flattern der Fahne in der Strömung -> Wirbelstrasse.
- Das Verhindern des Flatterns von Antennen und Blechschornsteinen durch das Anbringen von gewendelten Störkörpern.
- Der Golfball mit seinen eingedrückten Dellen und die historische Geschichte dieser Dimples dazu.
- Die Technik des Zustandebringens der Bananenkurve des Fussballs.
- Der Grund eines eventuell eiernden und flatterhaften Fluges hervorgerufen durch ein modernes Design der Fussballhaut.
- Die Umströmung eines Tischtennisballs und der Grund des stabilen Innehaltens im Luftstrom eines Föns.
- Die Gefahren von zuviel Stromlinienform am Auto.
- Die Wirkung des Spoilers am Auto, auch wenn er nur winzig klein ist.
- Die Umströmung eine Flugzeugflügels und die Auswirkung der verschiedenen Flügelformen.
- Das Wirbelsystem am Flügel.
- Der Magnuseffekt und die Demonstration mit einer rotierenden und nach vorn bewegten Rolle.
- Die Spielzeug-Schwirrflügelflugzeuge mit den drehenden „Flügeln“ am Strand.
- Die Gefahren der Randwirbelschleppe für die Luftfahrt.
- Der Vorteil des Verbandsfluges von Vögeln.
- Die Faktoren der Auftriebs- und Widerstandsformel und deren nützliche Beeinflussung für Start , Flug und Landung eines Verkehrsflugzeuges durch speziell eingestellte Veränderungen am Flügel. Der Auftrieb des Flügels muss bei jeder Geschwindigkeit immer das Gewicht des Flugzeuges ausgleichen und sich entsprechend anpassen.
Das waren die Betrachtungspunkte und ich hoffe, dass etwas Verständnis auch für manche Alltäglichkeiten vermittelt werden konnte.
04.05.2018:
Nach langer Zeit ging es heute weiter im Projekt. Die Osterferien, Klassenfahrt, Abwesenheit durch Teilnahme an der AERO 2018 und Krankheit führten zu diesem Arbeitsausfall.
Heute haben wir eine noch anstehende sehr lästige Arbeit erledigt. Die Traggestelle der Störklappen galt es noch zu entlacken. Dieses Rohrkonsrruktionen wurden vor Wochenmit einem Abbeizer eingepinselt und dann zum Wirken in Folie verpackt.
Die Farbe war nun perfekt abgelöst und konnte mit Schabern abgekratzt werden. Die Farbreste wurden dann mit Wasser abgewaschen. Ein letztes Bearbeiten mit einer rotierenden Bürste erfolgt noch.
Das Abnehmen der angelösten Farbe ging gut war aber dennoch ein Schmierkram.
Am Einbau der Steuerung wurde auch weitergearbeitet und die neuen Schrauben ausgemessen.
Ebenso wurde das in der letzten Werkstunde zusammengeklebte hintere mittlere Fussbodenbrett fertiggestellt.
==============================================================================
Ein neues Schuljahr und ein neuer Schüler der im Projekt mitarbeitet, diesmal aber total freiwillig nach dem Schuluntericht….. :-)))
Lasse fliegt im Luftsportverein Wilsche bei Gifhorn und besitzt auch reichlich Werkstatterfahrung. Herzlich willkommen im Projekt !
03.09.2018
Heute wurden die Deckel für die Störklappen gefertigt.
Die alten Störklappenabdeckungen, die aus einer 1,2 mm Sperrholzlage bestanden waren sehr beulig. Deswegen wurde beschlossen, dass die neuen Abdeckungen durch beidseitiges Auflaminieren von Glasfasergewebe, eine bessere Kontursteifigkeit bekommen sollen.
In der Werkstatt der Schule wurden gerade und beschichtete Spanplatten gesucht und gefunden :-), auf denen dann die fertig laminierten Sperrholzabdeckungen abgelegt werden konnten.
Die Auschnittsmaße der notwendigen Sperrholzstreifen für die Störklappen wurden auf der Sperrholzlage aufgezeichnet. Mit Hilfe eines festgespannten Lineals schneidet Lasse auf den Linien die Streifen mit Hilfe einer oszillierenden Säge heraus. Anschließend wurden die Sperrholzstreifen beidseitig leicht angeschliffen.
Auf einer anderen Werkbank wurden die notwendigen Glasgewebelage mit Übermaß zugeschnitten. Eine alte Abdeckung diente als grobes Maß für den Zuschnitt.
Nach der Fertigstellung der Sperrholzstreifen wurden diese mit Epoxydharz L160/H160 großzügig benetzt. Dazu diente eine Rollwalze aus dem Malerbedarf. Darauf kam dann die Glasgewebelage, welche sorgfältig aufgelegt und blasenfrei mit Harz getränkt wurde. Auf diese Glasgewebelage wurde noch eine Abreißgewebelage aufgelegt und wiederherum gut mit Harz durchtränkt. Abschließend folgte eine leicht steife Folie, die alles überdeckte. Mit einem breiten Spachtel wurde dann noch überschüssiges Harz unterhalb der Folie an den Rand des Holzstreifens gestrichen.
Danach wurde der einseitig laminierte Holzstreifen umgedreht und auf der anderen Seite auch mit einer Glasgewebelage beschichtet. Darauf kam dannaber direkt die Abdeckfolie. Leider reichte das mitgebrachte Abreißgewebe nur zum einseitigen Belegen von 4 Holzstreifen. Nach dem Abziehen der Abreißgewebelage wir diese nachher raue Seite der Abdeckung zum Aufkleben auf den Störklappenträger, der aus Metallrohren besteht und kleine Holzklötze beinhaltet, verwendet.
So geschah es mit allen vier Störklappenabdeckungen für unten und oben der beiden Flügel.
Leider haben wir keine Bilder beim Laminiervorgang gemacht -> vergessen !. Wir waren beide kontinuierlich am Arbeiten waren und hatten klebige Handschuhe an. Wäre alles natürlich möglich gewesen, aber leider wurde nicht daran gedacht… :-((
Wir haben zügig von 14:15 Uhr bis 17:30 Uhr gearbeitet. Es ist durch den Umstand der freiwilligen Mitarbeit von Lasse möglich, solange zu arbeiten bis wir mit dem was wir uns vorgenommen haben, fertig ist. Eine sehr zufriedenstellende Arbeitsweise.
Wir können hier nur noch den Presshaufen mit den schweren Holzbrettern darstellen, unter dem sich die 4 Sperrholzstreifen mit den beidseitigen Gewebelagen, befinden. Die Temperatur betrug an die 30 Grad und so wird eine schnelle Härtung eintreten.
15.10.2018
Das Besäumen der letztes Mal mit Glasgewebe belegten Sperrholzplatten für die Störklappen war heute angesagt und auch sollten die Rohrgestelle für diese Störklappen lackiert werden.
Mit der FEIN-Schwingsäge wurde die Ränder der Sperrholzplatten unter Zuhilfenahme eines Lineals von Lasse gesägt.
Hier ist eine ausgesägtes Abdeckplatte neben den unbearbeiteten Platten zu sehen. Das auf den noch zu besäumenden Platten zu sehende Abreisgewebe hat auch die bereits ausgesägte Platte, nur auf der anderen Seite. Das Abreißgewebe wird erst beim Verkleben der Platten auf die Rohrgestellrahmen entfernt. Das Verkleben der Abdeckplatten auf den Rohrrahmen wird später am Flügel passgenau vollzogen. Vorher ist dort noch eine Anpassarbeit der Platten an die Konturformen der individuellen Kastengrößen vorzunehmen.
Die andere Aktion mit dem Lackieren musste leider nach der Vorbereitung zum Spritzen abgebrochen werden, da der Lack nicht mehr in Ordnung war. Da hätte ich vorher genauer nachsehen müssen. Das hat mich schon gewurmt …. So mache ich das Lackieren jetzt zu Hause.
Stattdessen wurden die Rohre des Cabriorahmens auf der Helling auf Passgenauigkeit nachgearbeitet.
19.10.2018
Mit Vorbereitungen zum Bau der Sitzschalen und dem Einpassen der Holzstücke in die Störklappenrahmen wurde die Werkstunden des Freitag verbracht.
Die Störklappenrahmen wurden am Tag zuvor grundiert und konnten nun zum Einpassen der Holzstücke genutzt werden.
Mit einem in die Standbohrmaschine eingespannten Fräser wurden die alten Holzstücke aufgearbeitet und neue hergestellt und dann in die Rahmen eingepasst. Da die Rahmen alle geringfügig andere Maße , musste jedes Holzstück für seinen vorgesehenen Platz angepasst werden. Nach Nummerierung konnten die Holzstücke wieder ausgebaut werden. Der richtige Einbau erfolgt nach der Fertiglackierung der Rahmen und dem Grundieren der Holzstücke.
Die alten Sitzschalen werden durch neue ersetzt, da die bisherigen wegen wohl zu geringer Festigkeit in den 30 Betriebsjehren des Bergfalke mit reichlich GFK-Matten unterwärts verstärkt werden mussten. Die alten Sitzschalen dienen uns aber als Form. Die Schalen selbst werden aus zwei Lagen Sperrholz mit einer zwischengelegten 5 mm Tubusplatte hergestellt.
Hier sind die vorbereiteten Platten für den hinteren Sitz zu sehen.
Der vordere Sitz hat eine spärische Konturform im hinteren Bereich. Das wollen wir so lassen und nachbauen. In den tiefergelegten Bereich kommt die aus Aluminiumblech gefertigte Fallschirmschale. Diese Aluschale wird von Schülern der Heinrich Büssing Berufsschule in Braunschweig gefertigt.
Die durchgesessene Kontur des hinteren alten Sitzes musste erstmal aufbereitet werden. Das wurde mit viel Polyesterspachtel und dem 80 mm Exzenterschleifer von Metabo erledigt.
Der Metaboschleifer mit 80mm Schleifscheiben ist ein ideales, wirkungsvolles und sehr handliches Gerät und auch zum Schäften von GFK Bauteilen hervorragend geeignet.
Für das Formen der spärischen Kontur wurde die beiden Sperrholzplatten in ein Wasserbad gesteckt. Schaun wir mal, ob das dann am Montag mit dem Pressen in die alte Sitzschale unter Zuhilfenahme von einen GFK Formstück so klappen wird wie wir uns das gedacht haben.
22.10.2018
Der vorgesehene Arbeitsplan wurde fast abgearbeitet. Für die Weiterarbeit des Bespannens der Querruder war es außerhalb der Werkstatt zu kalt und in der Werkstatt geht es wegen der Geruchsbelästigung für die Kinder am nächsten Tag nicht. Vielleicht finden wir noch einen anderen Raum, sonst muss das im Aeroclub Braunschweig gemacht werden, da kennt man solche Gerüche….. 🙂
Die gewässerten Sperrholzplatten wurden mit Hilfe eines vorher abgeformten Schalen-formstücks aus GFK in den hinteren spärischen Teil der alten Sitzform gepresst. Das ging recht leicht und wir sind nun gespannt, ob die erzwungene Verbiegung im Holz bleibt. In einer Woche wird zum ersten Mal entformt, dann muss noch die Feuchtigkeit aus dem Holz entweichen, bis wir die Sitzschale mit dem Tubus verkleben können. Mal schaun wie das so klappt ….. 🙂
Die vielen Halteklötzchen aus Holz der Störklappenabdeckung wurden natur lackiert. Beim nächsten Werkeinsatz werden die Klötzchen in die dann fertige lackierten Rahmen eingebaut.
Der vordere alte Sitz wird zum darin erfolgenden Verpressens des Sperrholz-Tubus-Sperrholz Sandwiches, gegen das Verkleben zur Sitzform, mit Folie ausgelegt.
Auf der mit angedicktem Epoxyharz eingestrichenden unteren 1mm Sperrholzplatte wurde der Tubus bereits aufgelegt und in dem Bereich, wo beim Einsteigen in das Flugzeug mit den Füßen auf die Sitzfläche gestiegen wird, wurde die Tubuswabenlage mit einem extrem trockenen Mikroballoonspachtel zur Erhöhung der Druckfestigkeit ausgefüllt. Darauf erfolgte dann das Auflegen der oberen Sperrholzlage, die ebenfalls mit angedicktem Epoxyharz eingestrichen wurde. Der Mikroballoonspachtel wurde in der Art und Weise der Teigherstellung für Kekse gefertigt. Durch Kneten mit der Hand und Zugabe von Mikroballoons konnte die Masse sehr gewichtsreduziert hergestellt werden. Mit Rühren in einem Topf geht das nicht.
Weitere Bilder zu den Arbeitsgängen fehlen hier, da wir reichlich klebrige Hände hatten.
Die Sandwichplatte wurde dann in die alte Sitzform mit diversen Hilfsmitteln hineinge-presst. Zwischengelegte Schaumstoffplatten verteilen den Druck, da die Sitzfläche etwas gewölbt ist.
Holzleisten für den seitlichen Unterbau des hinteren Sitzes wurden zugesägt und werden bis zum nächsten Werktermin bei mir miteinander verklebt.
Anhand solcher Schablonen werden die weiteren Bauteile des Sitzes gefertigt.
29.10.2018
In der Zwischenzeit vom 22. bis zum 29. geschah:
- Die Störklappenrahmen wurden endlackiert.
- Die Holzzuschnitte für den Sitzunterbau wurden miteinander verklebt.
Die Tagesarbeit:
Die vielen Halteklötzchen aus Holz der Störklappenabdeckung konnten bei drei Rahmen mit angedickten Harz eingebaut werden. Die Zeit ließ es dann nicht mehr zu, den vierten Rahmen fertigzustellen. Beim nächsten Werkeinsatz wird das erledigt.
Die Holzleisten des hinteren Sitzunterbaus wurde zwischenzeitlich verklebt. Heute wurden die Holzteile zugeschnitten und mit den Befestigungsbohrungen versehen.
Die beim letzten Werktag geklebte und gepresste Sitzschale wurde ausgespannt und passt sehr gut zu den zuvor beschriebenen Unterbauteilen.
Das Verkleben der Sitzschale erfolgt später im Rumpf mit den dort montierten Unterbauteilen. Zuvor werden noch Erleichterungsbohrungen in diese Teile eingebracht und die Sperrholzplatten beidseitig aufgebracht, so wie beim Original.Die in der alten Sitzform sphärisch nass verpressten Sperrholzplatten wurden aus der Form genommen und müssen nun trocknen.
Vier Sperrholzplatten (1,2mm) für die Beschichtung der Unterbauleiste sowie weitere vier Sitzteile aus Sperrholz (links ist nur die Schablone zu sehen) wurden ausgesägt.
Je zwei Seitenteile für den Sitz wurden miteinander verklebt und verpresst. Rechts oben liegen schon zwei Teile übereinander und links unten ist das Harz auf der unteren Platte aufgebracht und das Teil links oben wird dann aufgelegt. Die Folie liegt unter und über den Teilen und verhindert das Verkleben mit den Formplatten.
Hier ist das Verpressen der Teile zu sehen
12.11.2018
Die 2 stündige Tagesarbeit umfasste:
- Fertigstellung des Einklebens von Montageleisten in den letzten vierten Störklappenrahmen.
- Modifizieren der seitlichen Unterbauspanten für den hinteren Sitz
- Fertigung gebogener Leisten.
1. Das Einkleben von Montage leisten in die Störklappenrahmen wurde beendet. Bilder dazu sind im letzten Report zu sehen. Die Störklappenrahmen werden für die Anbringung der Deckplatten in die Flügel eingebaut und vor Ort werden dann die platten befestigt. Das geschieht später bei der Weiterarbeit an den Flügeln in der erkstatt des Braunschweiger Aero Clubs.
2. Die Unterbauspanten für den hinteren Sitz wurde mit Erleichterungslöchern versehen, d.h. bisher nur einer. Der andere folgt demnächst. Diese Maßnahme soll der Gewichtserleichterung dienen. Zudem ist der Spant etwas dünner als der originale. Das unschöne Doppeloch wird noch korrigiert. Damit es nicht zu Festigkeitsverlusten kommt, haben wir zur Sicherheit einpaar Kohlefaserrovings auf der Unterseite aufgebracht.
Dazu wurden die beiden Spante nebeneinander gelegt und mit der Pappschablone in der Mitte und den späteren Sperrholzplatten an den Seiten eingefasst und mit Klammern pressend fixiert. Die Pappschablone und die Sperrholzplatten wurden mit Folie gegen ein Verkleben ummantelt. In diese zwei sich ergebenden Rillen (Unterseite der Spanten), wurden die getränkten Kohlefaserrovings eingelegt. Die Rillen wurde zuvor mit leicht angedicktem Harz ausgestrichen.
Zum Tränken der beiden Rovings wurden in ein mit Folie ausgelegtes Brett an beiden Seiten zwei Nägel geschlagen, um die der Rovingfaden von der Rolle mehrfach gelegt wurde. Damit werden die Rovings parallel ausgerichtet und während des Tränkens auch nicht verschoben.
Diese straff gespannten Rovings wurden mit Harz getränkt. Die Rovings wurden dannach auf beiden Seiten an der Längentrennmarkierung zerschnitten und in die oben beschriebenen Rillen eingelegt.
Mit einem aus Holz passend zugeschliffenen Spatel wurden die Rovings in die Rille gedrückt. Später nach dem Zerlegen der beiden Hilfsformkonstruktionen und dem Verputzen kommt da noch eine ganz dünne Kiefernleiste als Sichtobjekt darüber, bevor die seitlichen Sperrholzplatten aufgeklebt werden.
3. Aus vielen schmalen Sperrholzstreifen wurden zwei gebogenen Leisten aufgebaut, die später das hohe Seitenteil von außen gegen Biegung verstärken soll. Hier ist die Pressung von einer Leiste zu sehen. Mit dieser garnicht aufwändigen Baumaßnahme haben wir uns den Prozess von Wässern, Biegen und Trocknen gespart. Das Aussägen der 1mm dicken Streifen ging an einer kleinen Kreissäge schnell und auch das Verkleben und Anbringen an die mit Folie isolierten alten Formleisten, war ebenso schnell erledigt.
16.11.2018
- Ausbohren eines Sitzspantes
- Fertigung von einer gebogenen Leiste für den hinteren Sitz.
Der Arbeitseinsatz war heute sehr kurz, da nur eine Person anwesend war.
Das Verkleben der Sitzschalenteile für den vorderen Sitz erfolgt am nächsten Montag.
Der zweite Seitenspant des hinteren Sitzes wurde mit Erleichterungslöchern versehen. Die beiden zusammenfließenden Löcher mittlerer Größe des ersten Spantes vom letzten Arbeitseinsatz, wurden mit Holz wieder ausgefüllt und zwei kleinere Löcher wurden eingebracht. So sieht das besser aus :-))
Auf dem Bild ist unten der schwarze Kohlefaserroving zu sehen, der dem Spant noch eine zusätzliche Festigkeit geben wird.
Das Ziel ist, einen leichteren Sitz zu bauen, um das Rumpfgewicht zu reduzieren.
Für die Fertigung von zwei Leisten für die Aufnahme des Rückenbleches vom hinteren Sitz wurde eine einfache Holzform gebaut.
Hier ist schon eine ausgehärtete, aber noch unbearbeitete Leiste, vor der Form liegend, zu sehen.
Nach Auskleidung der Form mit dünner Folie (Frischhaltefolie) werden die mit Harz verklebten Sperrholzstreifen für die zweite Leiste eingelegt und mit Klammern an die Form gepresst. Die überhängende Folie wurde unter die Klammern gelegt.
Somit gibt es kein Verkleben mit der Form und dem Werkzeug.
19.11.2018
- Zusammenbau der vorderen Sitzschale
So wie geplant, haben wir uns heute auf den Zusammenbau der einzelnen Komponenten zur Sitzschale für den vorderen Sitz konzentriert.
In den alten Sitz ist bereits die mit angedicktem Harz eingestrichene untere Sperrholzlage und darauf das Wabenmaterial gelegt. Daneben ist das Kneten einer mit wenig Epoxydharz versetzten Microballoonmasse zu sehen. Wer schon mal Teig für Vanillekipferl gemacht hat, ist da im Vorteil 🙂 🙂
Die Masse wird in die Waben eingearbeitet und gibt später eine noch höhere Trittfestigkeit der Sitzschale. Beim Einsteigen in das Flugzeug treten diese Belastungen auf. Auf diese Schicht wird die obere mit Harz eingestrichene Sperrholzlage gelegt. Hier fehlen jetzt leider Bilder, da wir beide sehr klebrige Finger hatten.
Mit einem Brett, einer Halbrolle aus sehr dicker Pappe und zwei GFK Formstücke für die sphärischen Teile der Sitzschale wird die Sitzschale mit reichlich Schraubzwingen in der Form verpresst.
Nur an den Kanten, hier der sphärische Bereich, kann die Pressung kontrolliert werden. Zur Kontrolle der Verklebung in der Fläche werden wir eine thermographische Untersuchungsmethode benutzen. Über diese Untersuchungsmethode, warum und wozu noch notwendig, werden wir später mehr berichten …..
23.11.2018
Der ursprüngliche Plan, die hintere Sitzschale im Rumpf montiert zusammenzukleben, konnte nicht durchgeführt werden, da ich meine geplanten „Hausaufgaben“ aus Zeitmangel nicht machen konnte. So haben wir diese Arbeiten am Freitag weitgehend erledigt.
Sitzspanten hinterer Sitz
Verkleben der Sitzspanten mit einer Lage Sperrholz. Die inneren Sperrholzlagen wurden mit angedicktem Harz eingestrichen und die Spanten daraufgelegt. Das Sperrholz steht noch über und wird später passgenau abgeschnitten und geschliffen. Die äußeren Sperrholzlagen kommen erst nach dem Zusammenbau des Sitzes auf die Spanten und reichen bis Oberkante Sitzfläche.
Verpressen der Klebungen
Die verklebten Spanten wurden mit Folie beidseitig eingedeckt und dann mit weiteren Platten und Schraubzwingen gepresst.
Abschlussleisten hinterer Sitz
Die hintere Sitzschale erhält vorne und hinten noch eine Verstärkungsleiste. Diese Arbeit sollte ein Teil meiner vorbereitenden „Hausaufgabe“ gewesen sein, die jetzt erledigt wurde. Die Leisten werden sowohl die obere als auch die untere Sandwichschicht des Sperrholz-Wabe-Sperrholz Laminats bedecken. Hier im Bild ist das
Loslösen der unteren Sperrholzschicht zu sehen. Gesägt wurde mit einer Schwingsäge. Das sehr gut verklebte restliche Wabenmaterial wurde weggeschliffen. Die zum Einbau gefertigte Leiste liegt daneben. Diese Maßnahme erfolgt an beiden Sitzschalenenden (siehe weiter unten).
Seitenwangen hinterer Sitz
Der hintere Sitz hat zwei hohe Seitenwangen, die aus 2,5 mm Sperrholz bestehen. Die Seitenwangen halten die aus Aluminiumblech bestehende Rückfront des Sitzes. Beide Seitenwangen wurden als Paket zusammen auf der Dekupiersäge konturgerecht zugeschnitten und anschließend beschliffen.
Demonstrator
Für eine Erprobung von Fehlstellen in der inneren Verklebung von Sandwichstrukturen und auch deren Verklebung mit Rippen wurde mit dem Bau eines Demonstrators begonnen. Das Wabenmaterial wurde in zwei Stücken auf das mit Harz benetzte Sperrholz gelegt.
Eine kleine Ungenauigkeit wurde beim Zusammenfügen der Waben absichtlich eingebaut. Die Wabe wurde auf 1mm Sperrholz geklebt. ACHTUNG : Als Unterlage diente eine mit Folie abgedeckte Spanplatte !! Hier sieht es beim ersten Blick so aus, als ob wir die Wabe auf die Spanplatte geklebt hätten.
Vordere Sitzschale:
In die vordere Sitzschale muss im hinteren Bereich der gut gelungenen sphärischen Verformung auch eine Leiste eingebaut werden, durch die später Befestigungsschrauben gehen.
Hier im Bild ist die alte Sitzfläche und der Neubau mit zum Teil schon losgelöster Sperrholzlage zu sehen, um der Leiste eine Auflage auf der oberen sowie unteren Sperrholzlage zu geben. Ansonsten liegt die Sitzschale auf dem Rohrgestell und wird dort noch verschraubt.
03.12.2018
Leider war es immer noch schweinekalt in der Werkstatt, da seit Wochen die Heizung defekt ist….. :-((
Wir haben den Raum etwas erwärmt, indem wir zwei Türen geöffnet haben. Draussen war es angenehme 13 Grad „warm“ …. 🙂
Der schon lang ersehnte Plan, die hintere Sitzschale zusammen mit den Spanten im Rumpf zu montieren, wurde heute angegangen.
Die einseitig mit Sperrholz beplankten Sitzspanten wurden in die Rumpfhalterungen eingepasst. Es zeigt sich, dass es nicht so passte wie gedacht …. Normalfall … Bei der hinteren Schale war das Anpassen der vorderen Leiste am Sitz aber vorgesehen.
An verschiedenen Stellen wurde nachgeschliffen und auch die hinteren Befestigungslöcher der Spanten mussten um 8 mm versetzt werden, da sonst die durch den Tubusaufbau dickere Sitzschale auf den Rohren des Rumpfes aufliegen würde. Wenn die Spanten so geblieben wären wie sie mal in ihrer Geometrie waren, wäre das nicht passiert. So wurde die neue Schalendicke oben abgezogen und schon war unter der Schale kein Platz mehr zu den Rohren…. 😦
Das diverse Anpassen war aber keine Schwierigkeit, die alten Löcher wurden mit Holzdübeln klebend gefüllt und neue Löcher wurden gebohrt.
Hier ist bereits der Einbau der Spanten zu sehen. An den vier Aufnahme-punkten wurde Folie zum Schutz gegen das Verkleben dazwischengelegt.
Die Oberseite der Spanten sowie das zu verklebende Schalenteil wurden an den Kontaktstellen mit unverdicktem Harz getränkt und die Stellen nach den Einzug des Harzes wieder leicht abgewischt. Auf Spanten und Schale wurde mit Baumwollfaser und Stewathix (Thixotropiermittel, so wie Aerosil, aber nicht so staubig !) angedicktes Epoxydharz L160 (mit 25% H160) aufgebracht.
Grundsätzliches zu den Zuschlagstoffen:
Die Baumwollfaser oder ähnliche faserhaltige Füllstoffe bringen Festigkeit in die Harzmasse und sind damit Mikroverfestiger. Die Fasern verketten die Harzmoleküle. Vergleichbares wird heute mit eingemischten gröberen Faserstoffen im Estrich beim Hausbau gemacht.
Das Thixotropiermittel macht eine Masse zähflüssiger und verhindert somit das Auslaufen des Harzes aus einer mit Baumwollfaser angedickten Masse. Die Masse bleibt damit geschmeidig und ist nicht zu trocken. Die richtige Einstellung zum Verkleben mit dem Mittel ist erreicht, wenn die Harzmasse sich gerade nicht mehr vom Spatel bewegt.
Die Mikroballoons sind, wie der Name schon sagt, winzig kleine Hohlkugeln. Ein mit Mikroballoons eingedicktes Harz wird nur zum gewichtsreduzierten Verspachteln verwendet. Verklebungen dürfen damit nicht hergestellt werden, da die Harzmasse infolge der eingebrachten Miniblasen eine geringere Festigkeit bekommt, denn es ist eine Schaummasse entstanden.
Warum vorharzen ? : Bei der Verklebung sowie beim Spachteln mit Mikroballoons ist es stets wichtig, dass der zu behandelnde Bauteilbereich vor der Weiterarbeit mit unverdicktem Harz eingestrichen wird. Das Harz muss in das Holz einziehen können und der Überschuss wird abgewischt (das gilt auch bei angeschliffenen Faserverbundflächen). Wenn dies nicht gemacht wird, zieht das Holz das Harz aus der Masse und diese kann somit zu trocken werden. Besonders beim Spachteln mit hochangereicherter und damit sehr leichter Mikroballoonmasse kann das dazu führen, dass die Masse nicht mehr auf der Oberfläche haften bleibt.
Hier ist schon unser Werk im bereits wieder umgedrehten Rumpf zu sehen. Die Bauteile wurden mit vielen Klammern zusammengepresst. Die über-schüssige, herausquellende Harzmasse wurde sofort entfernt.
Wir müssen den Rumpf (umgedreht) immer außerhalb unserer Arbeitszeit auf der Wandhalterung ablegen. Der Transport dorthin mit all den Klammern ist gut gegangen … 🙂
Die vorhandenen Erleichterungslöcher der Spanten waren sehr hilfreich für das Zusammenzwingen. Die Spanten erhalten nach dem Planschleifen mit der Sitzschale, auf den Außenseiten noch weitere Sperrholzlagen.
Da Lasse schon eher für den Werkstatteinsatz frei hatte, konnten wir die Einbauarbeit gut schaffen. Weitere kleine Bauteile für den Fertigbau des vorderen Sitzes wurden auch noch hergestellt …… Ein guter Tag…. 🙂
Am 7.12. , 10.12. und 14.12.2018, fiel unser Werken leider aus ….
17.12.2018
Wir haben uns heute etwas mit der Thermographiemethode zur Feststellung von Fehlverleimungen beschäftigt. In vorangegangene Werkstunden haben wir ein Testobjekt hergestellt. Dies war eine kleine Sandwichplatte aus Sperrholz – Tubus – Sperrholz mit absichtlich eingebrachten Fehlstellen in der Harzverklebung und einer aufgeklebten Rippe. Wir haben diese Platte mit einem Wärmekissen aufgeheizt und dann geschaut, ob wir dort unsere Fehlstellen erkennen können, wo der Wärmeübergang etwas gestört sein sollte. Erahnen konnte man es, wenn man wusste, wo zu suchen war. Die Zeit war heute für eine intensivere Untersuchung und Modikiation von Wärmetzuführ zu knapp, da wir noch am Sitz die Sperrholzlagen aufbringen wollten. Ich werde zuhause weiterforschen, um zu lernen, ob die Erkennung mit entsprechenden Aufwärm- und Erkaltungsmaßnahmen zu verbessern ist. Mit wohl viel feiner auflösenden Messgeräten hat eine Abteilung des Fraunhofer Instituts in Braunschweig solche Fehlstellen an Flugzeugflügeln (Bericht liegt mir vor) gut sichtbar machen können.
Ich will nun erfahren, ob es auch mit dem mir zur Verfügung stehenden Handgerät funktioniert. Eine andere Methode mit Ultraschall, versuchen wir im nächsten Jahr.
Weiter ging es mit den Arbeiten am hinteren Sitz.
Der nun ausgehärtete hintere Sitz wurde aus dem Rumpfgerüst demontiert, was ohne Schwierigkeiten funktionierte. Die eingebrachte Folie hatte gute Dienste geleistet, nichts war verklebt. Nach dem Abschleifen der auf den Rippen überstehenden Sitzfläche
wurde das Tubusmaterial am Rand etwas in der Tiefe ausgefräßt, die Rippen und das Sperrholzteil für die zu machende Abdeckung mit Harz getränkt, wieder abgewischt, die Rippen mit Baummwollfasern und Stewatix leicht angedicktem Harz eingestrichen und
schließlich das Sperrholzteil aufgebracht. Das geschah auf beiden Seiten. Die Sperrholzlagen wurden mit Folie, beigelegten Hölzern und mit Hilfe von Leimzwingen auf die Rippen gepresst. Überschüssiges Harz wurde entfernt.
Das kann nun gut aushärten — Dank der Heizung, die wieder tätig ist —
07.01.2019
Heute haben wir an dem hinteren Sitz weitergebaut. Nach dem Verputzen der überstehenden Sperrholzteile wurde es etwas schwierig … Die hinteren beiden Seitenwände für zur Aufnahme der Rückwand für den Fallschirm sollten angebaut werden. Das Ausrichten hatte so seine Tücken.
Letztlich waren die beiden Seitenteile verlässlich ausgerichtet und mit Nägeln verstiftet, aber die Zeit zum Verkleben war nicht mehr gegeben, da Lasse zum Bahnhof musste. Er wohnt weit außerhalb von Braunschweig und 40 Minuten vor Abfahrt des Zuges um 17 Uhr räumen wir alles zusammen und danach wird Lasse zum Bahnhof gebracht.
11.01.2019
Man hatte sich vorgenommen, die Seitenteile des hinteren Sitzes in der Zwischenzeit zu verkleben, aber dann kommt immer wieder der unvorher-gesehene Tagesgeschäftsteufel dazwischen und schon ist wieder der nächste Werktag da….. 😦
Egal, nach der guten Vorarbeit mit dem Verstiften konnte heute nach den Anschleifen des Sperrholzes die hohen Seitenwangen der Rückenlehne mit dem Sitz verklebt werden.
Hier bereits verklebt, verklammert, verpresst zum Aushärten abgelegt. Überschüssiges und herausquellendes Harz in den Ecken wurde mit Aceton entfernt, damit die Holzfläche des Sitzes sauber bleibt und später mit Fussbodenparkettlack natur behandelt werden kann.
Eckbleche der Haube
Weiter ging es dann mit den Vorbereitungen zur Fertigung der schmalen und langen Eckbleche, die nach dem Verglasen der Haube auf die Kanten der eckigen Bergfalkehaube geschraubt werden und dabei die Plexiglasplatten halten und auch die Stöße abdichten sollen. Diese Eckbleche waren nicht mehr da.
Wir haben zum Aufbau der Form für das Biegen und Treiben der Bleche, den Haubenrahmen benutzt und ihn mit 4 mm Hartfaserplatten verkleidet. Das entspricht etwa der Verglasung, etwas dicker aber das ist egal.
Das Metallgerüst wurde an den Kontaktstellen mit Papiertape beklebt, um dem verwendeten Heißkleber eine Haftbasis zu geben. Der Heiskleber wird sehr schnell an einer ungewärmten Metallfläche durch die rasche Temperaturableitung hart und klebt deshalb nicht gut. Hier hilft etwas das Tape. Zudem wird dabei auch nicht das Rohrgestell mit dem Heißkleber beklebt, der von der Machart der Klebepistole sehr heiß ist.
Verwendet wurde eine Profiheißklebepistole mit 100 Watt Heizleistung. Das ist ein ganz anderes Kaliber als die üblichen Klebepistolen aus dem Baumarkt mit vielleicht 20 Watt. Damit wird der Kleber schon richtig heiß, dass auch große Vorsicht bei Hautberührung geboten ist. Das sonst so schnelle Auskühlen der Klebemasse am Metall wird bei den hohen Temperaturen gemindert.
So wurde der Haubenrahmen an den Seitenflächen und der Deckfläche mit den Hartfaserplatten eingeschalt.
Die Haubenkanten wurden nicht bündig angepasst. In den Kanten war also ein kleiner Spalt. Dieser Spalt wurde mit Polyesterspachtel ausgefüllt, der dann eckgerecht geschliffen wird.
Das Schleifen der Kanten erfolgt am Montag, den 14. Januar.
14.01.2019
Die mit Polyesterspachtel ausgefüllten Kanten der Haubenform wurden mit einem kleinem ( 80mm Metabo) Rotationsdschwingschleifer ausgearbeitet.
Nach einer gründlichen Reinigung der Oberfläche mit Aceton, wurden um die Kanten Packtape geklebt
und anschließend dieser beklebte Bereich mit Wachs als Grundierung für flüssige Trennfolie behandelt.
Das Ziel der ganzen Arbeit mit dem Bau der Haubenform ist die Fertigung einer Form zum Biegen der winkeligen Kantenbleche für die Abdeckung der Haubenkanten.
Die Verwendung der flüssigen Trennfolie hat den Vorteil, dass das hergestellte Formteil auf der inneren Seite, der Seite von der Formgebung, kein Wachs an der Oberfläche hat sondern eventuell nur dieses Trennfolienmaterial. Dieses Material ist einfach mit Wasser abzuwaschen.
Nach dem Ablüften der Trennfolie konnte laminiert werden. Auf den beiden Haubenkanten wurden 5 Lagen 92125er Gewebe diagonal aufgebracht. Diagonal deswegen, weil die Glasfasern sich so leichter um die Kanten legen lassen und kein Gewebeabheben eintritt. Die Kante der Form ist dazu auch nicht genau eckig geschliffen, sondern leicht gerundet worden !!
Die diagonal geschnittenen Gewebestreifen wurden unverzogen (!) auf eine Papprolle locker gewickelt und dann am Formkörper wieder locker abgewickelt, ohne dass sich das Gewebe verzieht. Auf das Auflegen von Abreißgewebe wurde verzichtet, da der Polyesterspachtel auch so gut haftet.
Diese Formteile werden am Freitag mit Polyesterspachtel („Autospachtel“) geglättet und dabei werden natürlich die Kanten diesmal genau kantig geschliffen.
Die fertigen Formteile werden dann mit Spanplatten unterstützt. Dann kann darauf das Alu-Blech formgetreu gebogen (getrieben) werden.
Während Lasse das Ablüften des Trennmittels mit einer Heißluftpistole (nur leicht warm), das Harzanmischen, das Zuschneiden des Gewebes und das Laminieren hauptsächlich durchführte, konnte ich die noch fehlenden vier Stützstreifen an den Seitenteilen ankleben …. Bild fehlt hier leider …. und dann uch noch beim Gewebeauflegen und Harzen mithelfen.
18.01.2019
Zwei Arbeiten haben wir heute durchgeführt: Weiterarbeit am hinteren Sitz und an dem Formkörper zum Biegen der Haubenkantenbleche.
Lasse sägte am hinteren Sitz überstehende Sperrholzlagen ab und verschliff die Ecken und Kanten. Dem Sitz fehlen nun noch einige Spanten unter der Sitzfläche und eine Abschlussleiste am oberen Teil der Seitenwangen zur Aufnahme des Alubleches der Rückseite.
Das war das Abschlussbild der letzten Werkstunde, die aufgebrachten Glasfaserlagen für den Formuntergrund zum Biegen der Kantenbleche für die Haube.
Reichlich Polyesterspachtel ( „Autospachtel“ ) wurde auf die Glasfaserlagen aufgebracht. Nach der kurzen Aushärtezeit konnten mit einen Bandschleifer
die Haubenkantenform geschliffen werden. Das staubte, trotz Staubbeutel, mächtig und der persönliche Schutz musste durch die Atemschutzmasken gewährleistet werden. Die Flächen der Haubenverkleidung dienten dabei sehr gut für die Führung der Bandschleifmaschine. Die Kanten wurden kantig ausgeschliffen. Ob das so bleibt, oder wir brechen noch etwas die Kanten, wird sich beim Biegen zeigen. Das hängt von der Güte des zu beschaffenden Bleches ab.
Der Plan, die gefertigten GFK-Kanten abzunehmen und mit einer Spanplatte zu unterstützen, damit dann dieser Träger in der Werkbank festgespannt werden kann, wurde kurzfristig aufgegeben. Lasse überzeugte mich schnell, dass doch die Haube stabil genug sei, um daran biegen zu können. Im Holzlager der Schule fanden wir schnell eine Spanplatte, die uns als Unterbau dienen konnte. Mit Unterstützungsklötzen wurde der Haubenrahmen darauf festgelegt.
Das war es für heute … Wieder einmal ein Super Teamarbeitstag !!!!! Morgen wird Alublech beschafft und am Montag begonnen, die Bleche zu kanten.
22.01.2019
Heute war das Lernen des Biegens von Alublech an einer sphärisch gekrümmten Form angesagt. Mit der Fertigung der für die Kanten der Haube notwendigen Abdeckungsbleche wurde begonnen. Es war heute vornehmlich ein Lernprozess.
Mit einem Blechknabber, der an einer Bohrmaschine angeschlossen wird, wurden die notwendigen Blechen nach Schablone ausgeschnitten.
Die Blechstreifen sind breiter als notwendig. Auf das genaue Maß werden die gekanteten Bleche später mit der Schwingsäge geschnitten und mit Schmirgelleinen geschliffenDer Blechsteifen wird an die seitliche Haubenkante festgeklemmt und auf der Oberseite umgebogen und mittels Holzklotz und Hammer glatt gehämmert. Dabei gibt es Beulen, da das umgelegte Blech durch die Formgebung der Haube oben gestaucht wird.
Hier ist das ausgeschnittene Blech an vorderen Haubenbereich festgeklemmt und noch ungebogen zu sehen. In diesem Bereich ist die Krümmung besonders stark und da gibt es dann erheblich mehr Stauchungen, die sich in Beulen auf der Oberseite bemerkbar machen.
Das ist das Resultat: Ausbeulungen, die nur durch ein Stauchen des Blchmaterials zu entfernen sind.
Dazu werden die eng neben der Beule gelegenen Blechbereiche mit Hölzern und Schraubzwingen festgelegt und die dazwischen befindliche Beule wird mit einen Holzstück und Hammer bearbeitet.
Das klappt bisher sehr gut, wie hier vielleicht zu sehen ist. In dieser Art und Weise muss Beule für Beule gestaucht werden.
Wir haben heute viel gelernt und werden am nächsten Freitag mit dem Biegen der Bleche weitermachen.
25.01.2019
Nachdem wir am letzten Werktag die Bleche für die Eckenverkleidung der kantigen Haube vom Bergfalken II zugeschnitten hatten und erste Lernerfolge beim Dengeln des Aluminiumbleches erzielen konnten, ging es heute mit diesem Wissen mit den anderen noch zu biegenden Blechstreifen weiter.
Die Blechstreifen werden mit etwas Überstand gebogen, was etwas nachteilig dazu führt, dass das zu verformende Teil des Kantbleches schwieriger zu bearbeiten ist. Außen muss mehr gestaucht werden.
Denn das Dengeln der Kantbleche ist infolge der Haubenkontur kein Treiben des Bleches sondern ein Stauchen. Das Blechmaterial im Bereich der entstehenden Beulen muss verdichtet werden. Mit dem Festhalten des Bleches beidseitig ganz dicht neben der Beule, kann das „überschüssige“ Material der Beule durch Hammerschläge verdichtet werden …. die Beule ist weg … :-))) Zwischen Hammer und Beule wird ein Hartholzklotz gelegt, der gerundete Kanten hat.
Zuschneiden der Blechkanten:Das reichlich überstehende Blechmaterial der Haubenseitenfläche wird mit einer Schwingsäge abgeschnitten. Das Blech der Oberseite wird beim Biegen stets enger gefasst, aus den oben beschriebenen Gründen wegen des Verdichtens. Das überstehende Blech von der Oberseite (zeigt hier nach unten) ist hier schon abgeschnitten worden und wird hier knapp mit der Hobelbank festgehalten.
Voilà …. es passt…. :-))) Dieses vordere Kantenstück war wegen der starken Krümmung anspruchsvoll in der Herstellung. Wenn solch ein Teil zu fertigen ist, werden wir die anderen Teile auch schaffen. Alles Übungssache 🙂 Die Weiterarbeit, mit dem Kanten der Bleche, wird erst wieder am 4. Februar erfolgen.
04.02.2019
Es gibt über den heutigen Werktag nicht viel zu berichten. Die Abdeckbleche für die Haubenkanten wurden weiterbearbeitet. Die Arbeit ist im Prinzip auf den Bildern des letzten Werktages zu sehen. Dazu bitte Herunterscrollen bis rote Felder erscheinen. Eine neu gestaltete Webseite für unseren Blog ist von Lasse in Arbeit und wird demnächst das Projekt übersichtlicher präsentieren.
Einige Schraubzwingen haben uns heute etwas geärgert, da die Spannarme der Zwingen keine gute Klemmung hatten. Beim Dengeln lösten sich die Klemmungen und die Zwingen fielen ab.
Es ging dann nur zu zweit weiter: Der eine dengelte der andere kontrollierte die Schraubzwingen und zog die Schraubung nach, wenn es nötig war. Irgendwie verging heute die Zeit dabei recht schnell, bis wieder Aufräumen und Einpacken angesagt war, damit Lassse rechtzeitig zum Bahnhof für die Heimfahrt nach Gifhorn kam. Es fährt leider nur alle 2 Stunden ein Zug direkt nach Gifhorn.
Das ist das Abschlussbild des heutigen Tages, damit es überhaupt ein Bild gibt :-)) : Das eingespannte Blech für den vorderen Haubenkantenbereich auf der linken Seite, schon etwas umgebogen und die erste Beule zeigt sich bereits. Die Arbeit werden wird dann wieder gemeinsam am nächsten Montag machen und ich ahne schon, vielleicht sind wir auch am darauf folgenden Werktag noch damit beschäftigt. Die Arbeit dauert länger, als ich geplant hatte. So isses manchmal ….. oder oft … 🙂
15.02.2017
Das letzte Blechteil der Haubenkantenverkleidung von vorne links wurde gemeinschaftlich bearbeitet. Meine Mitarbeit bestand aus der Mithilfe des Setzens der Schraubzwingen dicht an den Beulen, die unterwärts immer noch Abstandsklötze benötigten. Das geht dann nur gut zu zweit.
Anschließend wurden beide GFK Formteile der Kanten abgenommen und das Haubengestell von der Presspappenverkleidung befreit.
Hier ein Bild von den Andruckhölzern neben der Beule zum Festhalten des Bleches zwecks Verdichtung des Alubleches durch Hammerschläge, mit einem Hartholzklotz dazwischen. Die Hölzer können auch noch dichter an der Beule sein.
Wir werden noch einen mobilen Blechbeulenvernichter herstellen, um Beulen noch nachträglich an dem später nun sehr schmalen Verkleidungsblech eleminieren zu können. Mal nachdenken …..wie … 🙂 Wir berichten dann .. 🙂
18.02.2017
Das Zuschneiden der bisher gebauten Haubenkantenleisten wurde auf später (oder zuhause ….) verschoben. Für die Haube ist jetzt das Plexiglasmaterial zu beschaffen, dann könnten nach dem Zuschneiden der Plexiglasplatten die dann fertigen Haubenkantenleisten der geschlossenen Haube montiert werden. Mal schaun, ob wir dann die Kantenleisten noch nachbiegen müssen. Ein spezielles Werkzeug wird dafür hergestellt. Der Rahmen der Cabriohaube ist noch im Bau.
Heute wurden Kleinteile für den Rumpf gefertigt.
Für den hinteren Sitz wurde das Rückenteil aus Alublech ausgeschnitten. Hier muss dann noch die obere Holzleiste gefertigt werden. Dieses Blech wird dann mit kleinen Holzschrauben befestigt. Nicht leicht, diese im Handwerkshandel zu erhalten. Der erste Anlauf schlug fehl 😦
Der Bergfalke ist ja sehr fortschrittlich: Die Verbindungen zu den Bremsklappen im Flügel sind Selbstanschlüsse. Für diese Torsionsanschlüsse sind beidseitig Löcher in der Rumpfbespannung vorzusehen. Um dieses Loch zu verstärken werden Sperrholzplatten mit zentralem Loch auf das Rohrgestell geklebt, die später mit der Bespannung überzogen werden.
Hier ist das kleine Tagwerk zu sehen. Sieht echt wenig aus …. die Zeit wurde aber gefüllt. Die Sperrholzplatte mit dem kleinen Loch wird in dem Bereich der Befestigungsschraube vom Höhenleitwerk auf dem Rumpfgestell montiert. Dort läuft die obere Konturleiste aus und ist auf der Platte aufgeleimt.
Die noch aus dem Urzustand des Flugzeuges gut erhalten gebliebenen Formleisten werden, wegen der Beschädigungsgefahr beim Hoch- und Runterhieven des Rumpfes von seinen Ablagegestell, erst ganz zum Schluss vor dem Bespannen montiert.
22.2.2019
Eine erfreuliche Nachricht kam von der Waldorfschule. Bis zum Ende des Schuljahres, incl. den Sommerferien, haben wir den Werkraum alleine nur für uns.
Das bedeutet, dass wir das Rumpfgestell unten lassen können und nicht bei jedem Arbeiten herunterlassen und am Ende wieder hoch auf die Ablage hieven müssen.
Lasse hat ein Sperrholzbrett, auf dem später die obere Rumpfkonturleiste aus Holz aufgeleimt wird, passgenau bearbeitet und mit dem Hochleistungskleber Araldit eingeklebt.
Die Fussbodenbretter für den hinteren Sitz wurden bezüglich der Befestigungslöcher nachgearbeitet. Das geplante Einsenken und „Einkleben“ der Senkschrauben konnte leider nicht durchgeführt werden, da ich einen Gewindeschneider nicht eingepackt hatte. Das Gewinde der rumpfseitigen Muttern war noch mit Farbe zugeschmiert. Unter „Einkleben“ der Senkschrauben ist folgendes zu verstehen: Da die Fussbodenplatten aus einem Sandwich (Sperrholz, Wabe, Sperrholz) besteht, wird die Senkschraube in den Bereuich des Wabenmaterials verschwinden. Die obere Sperrholzschicht wird also ein Loch von der Größe des Schraubenkopfes haben.
Der Auflagebereich des Senkkopfes wird in der Wabe mit angedicktem Harz (Baumwollschnipsel und Tixotropiermittel -> Aerosil oder Stevatix) ausgefüllt. Die Wabe ist dazu etwas auszufräsen. Die Harzmasse wird auch unter die obere Sperrholzschicht gebracht damit diese im Verbund mittragen kann. Die Schraube ( für die Anpassmontage Inbus oder Torx wegen des besseren Herauslösens als die spätere Schlitzschraube) und die am Rumpfgestell angeschweißte Mutter wird mit Trennwachs behandelt und eingesetzt. Zwischen Mutter und dem Bodenbrett wird noch Folie gelegt, die im Bereich der Mutter durchstochen wird. Das machen wir dann am nächsten mal.
Hier brauchen wir noch Rat. Da wir keinen Bergfalken als Anschauung vor uns haben und auch diesen Bergfalken nicht abgeledert haben, interessiert uns die Anbringung der Lochverstärkung für den Störklappenanschluss. Unseres Erachtens wäre das in dem oberen Bild Dargestellte richtig. Das Sperrholzbrett ist nur oben festgeklebt und ist parallel zu der Linie Rohr Konturleiste. Die Bespannung wird dann darauf geklebt.
Das komplette Höhenleitwerk (in den Pappkisten gut geschützt) wurde in der Zwischenzeit in die Werkstatt geholt. Wir haben jetzt ja Platz 🙂 Am Leitwerk ist auch noch was zu reparieren.
01.03.2019
Entgegen der Planung haben wir uns heute zuerst der Reparatur der Höhenleitwerksfinne angenommen. Ein kurzer Bericht …. :
Auf der Oberseite war ein größeres Loch, dass für die Reparatur bis zu den angrenzenden Spanten vergrößert wurde. Das Sperrholzstück für die Reparatur war weitgehend schon von einem Segelfliegerkameraden vorbereitet worden, aber bislang nicht eingebaut worden. Es galt nun noch Nagelleisten herzustellen und weitere Schäftnacharbeiten durchzuführen, da das Sperrholzbrett einen bestimmten Bereich nicht bedeckte, der auch noch zu reparieren war. Statt ein komplett neues Sperrholzstück anzufertigten, entschlossen wir uns, das vorhandene und vorbereitete Material einzubauen und später noch einen schmales Stück nachträglich einzuleimen.
22.03.2019
Heute hatten wir von 13:45 bis 19.30 Uhr viel Zeit, da Lasse danach noch einen Einsatz in der Schule hatte.
Der Neubau des vorderen Fußbodenbrettes wurde angegangen. Das Brett wird wie schon die hinteren Bretter auch, als Sandwich aus Sperrholz und Tubuswabe hergestellt.
Nach dem Zuschneiden der Sperrholzbretter wurden an den Stellen, wo später die Befestigungsschrauben sitzen sollen, kleine Sperrholzscheiben von der Dicke des Tubus eingebracht.
Ebenso eine Sperrholzausfüllung an der Stelle, wo die vordere Seitensteuer-Pedal-Verstellung zur Fixierung einrasten kann. Verklebt wurde alles mit Epoxydharz.
Danach folgte das Einlegen des Tubus und die andere Deckschicht.
Abschließend ein dickes Brett mit Folie draufgelegt und fertig ….
Die Löcher für die hinteren Fussbodenbretter wurden vor Ort mit in Harz eingesetzten Schrauben genau bestimmt. Hier hatten wir die Lochverstärkung im Tubus mit angedicktem Epoxyharz angewandt. Etwas aufwändig. Bei dem heute gebauten vorderen Brett wurde Sperrholz in den Tubusbereich der künftigen Verschraubung eingebracht.
Die Löcher wurden mit einem Senker so bearbeitet, dass die
die Senkschrauben glatt mit der Oberfläche abschließen.
In einer weiteren Aktion haben wir die metallenen Halteelemente der Seitenformleisten auf die schon länger eingebundenen Holzleisten geklebt und den geraden Verlauf der Leisten eingestellt.
Das geplante Verschrauben der Aluplatte an der Rückseite des hinteren Sitzes wurde zurückgestellt, da der passende Torxschraubendreher nicht dabei war. So wurden nur die Löcher in die Platte schon mal gebohrt.
Vielleicht noch etwas früh, aber die Instrumentenbretter brauchen wir schließlich auch mal. Lasse hat mit der Erstellung einer ersten Schablone für das vordere Brett begonnen.
29.03.2019
Heute hatten wir einen „Normalwerktag“ von 13:45 bis 16.30 Uhr.
Das beim letzten Werken zusammengeklebte vordere Fussbodenbrett hat Lasse an den Kanten beschliffen. Das Verbohren für die Befestigung erfolgt am kommenden Montag.
Zwei kleine Schäftungsstellen an der Höhenleitwerksfinne wurden für das Verleimen vorbereitet.
Die Alurückwand des hinteren Sitzes konnte nun endlich nach Fertigung eines überlangen 2mm Bohrers mit Hilfe eines passenden Messingrohres und Sekundenkleber, angeschraubt werden. Zum senkrechten Vorbohren dicht an der Seitenwand war der Bohrer notwendig. Die Beschaffung eines winzigen Torxbitkopfes für die Schrauben gelang auch.
Den Schablonenbau für die Instrumentenbretter und zwei Sperrholzverkleidungsstücke um die hinteren Querkraftbolzen, zwecks verbesserten Aufbringens der Rumpfbespannung, hat Lasse noch in Arbeit.
1. April 2019
Heute war ein Sonderwerktag, da die Waldorfschule bereits diese Woche mit den Osterferien begonnen hat. Lasse reiste extra dafür an und ich holte ihn am Bahnhof an.
Das Einpassen der Instrumentenbretter machte Fortschritte. Das vordere und das hintere Brett wurde bezüglich seiner Abmaße zum Rumpf und zu den Befestigungspunkten fertiggestellt. In den folgenden Werkstunden werden die Instrumente positioniert.
Der hintere Sitz bekam eine obere Abachlußßleiste in der ein Schlitz für das Rückenblech ist. Die Folie soll das Ankleben des Bleches verhindern.
Das vordere Fußbodenbrett wurde verbohrt und verschraubt.
Zwei kleine Reparaturschäftungen an der Höhenleitwerksflosse wurden verleimt.
Beim vorderen Sitz haben wir mit dem Finden der Löcher und Verbohren für die Befestigungsschrauben angefangen.
So langsam komplettiert sich die Inneneinrichtung. Obwohl hier noch einiges zu tun ist, werden wir uns in den nächsten Werkstunden mit der Fertigstellung der Bespannung der Querruder befassen.
Wir müssen die Ferienzeit nutzen, da wir wegen des Klebelackgeruches keinen belästigen können.
Das hat leider durch Ausfälle nicht geklappt :-((((
28. Mai 2019
Nach langer Pause ging es heute weiter. An vielen Kleinigkeiten wurde gearbeitet.
Für den vorderen Sitz mussten die Befestigungslöcher gesucht, gebohrt und gesenkt werden. Lasse hat das problemlos hinbekommen. In der nächsten Werkstunde wird vorne über dem Rumpfrohr noch eine Leiste angeklebt.
Die Tubusränder der Sandwichplatte (Sperrholz-Wabe-Sperrholz) wurden mit Microballonspachtelmasse ausgefüllt. Verschliffen wird in den nächsten Werkstunden.
Eine kleine Beschädigung an der Hinterkante der Höhenruderflosse wurde mit einem Stück eingeschäftetem Sperrholz repariert.
Die hintere Sitzschale bekommt unterwärts noch Versteifungsleisten, da dort kein Rumpfgerüst die Sitzfläche unterstützt. Lasse hat diese Bauteile schon vorbereitet, die beim nächstes Werken eingeklebt werden. Hier ist der eingelegte Zuschnitt der Leisten in die Rückseite des Sitzes zu sehen.
Um die hinteren Querkraftbolzen des Rumpfes hat Lasse Sperrholzplatten gefertigt, damit später beim Bespannen dort eine Auflage für den Stoff vorhanden ist. Angeklebt werden die Holzteile erst, wenn die seitlichen Formleisten fest montiert sind.
3. Juni 2019
Mit diversen Kleinarbeiten ging es heute weiter.
Ich hatte die alten Instrumente für die Instrumentenbretter mitgebracht. In der Aufbewahrungskiste war auch das Venturierohr enthalten.Lasse bohrte und fräste dafür die entsprechenden Löcher in die vordere Rumpfverkleidung, wo sich darunter die Befestigungssstelle befindet.
Noch die passenden Schrauben besorgen, das Rohr reinigen und alles wieder zurück in die Kiste für die Endmontage.
Lasse machte sich dann an die Weiterarbeit der Instrumentenbretter … anzeichnen, aussägen und mit einem großern Rundschleifer das finale Anpassen der Ausschnitte.
Voilá … Die ersten Löcher sind eingepasst … Die Instrumente (wir brauchen keine 2 Fahrtmesser vorne …. nur Muster hier.. :-))) passen. Nächsten Mal geht es weiter. Der Kompass und die Funke müssen noch Ihre Löcher bekommen.
An dem vorderen Sitz wurde vor Ort vorne noch eine Leiste montiert.
Unterhalb des hinteren Sitzes wurden die vorbereiteten Verstärkungs-leisten eingeklebt.
17.06.2019
Den letzten Freitag habe ich ausfallen lassen, da Lasse mit der Schule sehr beschäftigt war und es mir auch besser passte. Es muss aber weitergehen und so war ich allein am Montag in der Werkstatt für kurze Zeitr und habe diverse kleine Arbeiten erledigt:
- Genaues Anpassen der Bodenbretter, da war noch was wegzusägen –> das reduziert Gewicht 🙂
- Diverse Weiterarbeit an den Sitzen: Der hintere Sitz musste im vorderen Teil noch Auffüllklötze an den Befestigungsstellen bekommen.
- Einige Zusatzverstärkungen wurden vorbereitet, die nächstes Mal angebaut werden, wenn die Sitze montiert werden können.
- Blechteil herausgesucht für den Antennenanbau.
21.06.2019
Für die Handhabung des Rumpfes (Umdrehen) mit zwei Personen ist der Rumpf im vorderen Bereich durch die Verkleidungen nicht mehr gut zu händeln. Um dies wieder sicher zu ermöglichen, wurde heute eine Lösung eingebaut. Im Rumpf wurde eine Spanplatte an den Befestigungspunkten des Instrumentenbrettes und unten in dem gelochten Rohr der Pedalverstellung solide montiert. Ein Holzstab führt durch die vordere Rumpföffnung für die F-Schleppkupplung (Kupplung ausgebaut) zu dem Brett und wurde damit verschraubt. Jetzt können wir den Rumpf mit 2 Personen sicher drehen und die Formleisten können fest montiert werden.
An dem hinteren Sitz mussten noch Anpassarbeit an den Befestigungspunkten stattfinden. Das war ein Fummelkram, der mit viel Aus-und Einbauen verbunden war. Nun passt es und die nächsten Arbeitsschritte an den Sitzen liegen noch bei denj vorderen Sitzabschlüssen….. Das nächste Mal …
Die Antenne wird nach alter Art am Baldachin sichtbar nach außen angebaut. Ein Alublech dient zur Basisbefestigung der Antenne. Lasse hat nach Fertigung einer Pappschablone das Blech zugeschnitten und das Montageloch für die Antenne gebohrt. Das Loch kann sich leider nicht mittig befinden, da dort eine Formleiste zu montieren ist.
Sehr formschlüssig für die spätere Bespannung wurde das Blech mit Aradite 2014 eingeklebt.
Die Termine der nächsten Werkstunden können nicht vorhergesagt werden, da demnächst die Sommerferien beginnen und Lasse bis dahin mit anderen Arbeiten beschäftigt ist. .
SOMMERFERIEN
22.08.2019
Die Sommerferien in Niedersachsen sind vorüber und die Schule hat wieder geöffnet. Lasse hat am Donnerstag nach der Schule Zeit und so wird ab 15:30 Uhr am Bergfalken weitergearbeitet. Arne hat sich gemeldet, schaute vorbei und half gleich mit. Arne hatte vor Lasse am Projekt mitgearbeitet, vor einem Jahr die Schule verlassen und macht jetzt eine Ausbildung zum Steinmetz. Sein Ziel ist es, als Restaurator im Steinmetzwesen später einmal zu arbeiten. Ich war sehr erfreut, dass er noch Interesse an den Projekt hat, obwohl er kein Schüler der Waldorfschule mehr ist.
Heute war das Annieten der Formleisten geplant. Die Alu-Nieten zum Schlagen hatte ich besorgt. Popnieten wollten wir aus historischen Gründen nicht nehmen.Arne und Lasse machten die Arbeit hervorragend. Die Nietlöcher im Blech und der Holzleiste wurden vor den Hineinstecken der Nieten mit dem passenden Bohrer „harmonisiert“ …..
Der Rumpf lag auf dem Rücken. Der Niet wurde von unten durch die Bohrung der Befestigungslaschen gesteckt. Ein schwerer Stahlklotz mit einer Rundkopfvertiefung wurde unter den Niet gehalten und von oben dann der aus dem Blech herausragende Niet mit dem Hammer etwas gestaucht.
So schaut es dann aus, wenn es fertig ist. Da der Rumpf auf dem Rücken liegt, ist das also die Unterseite der Vernietung.
Neben dieser Arbeit wurden noch zwei Leisten für den Fußbodenausbau des hinteren Sitzes gefertigt. Gefertigt: Die Leisten waren mit vielen Erleichterungsbohrungen versehen und wurden mit Sperrholz verkleidet. Schaun wir mal, was das bezüglich des Gewichtsgewinns gebracht hat…. oder nur guter Wille …?
Bei Arbeiten von mir während der Ferien wurde neben Anpassarbeiten an den Sitzen (immer noch nicht ganz fertig) auch die Antenne mal probemontiert. Eine Antenne nach alter Tradition … muss so sein. Das schöne Ding hat mir Mario Selss gegeben.
Kleine Nacharbeiten bei dem Vernieten erfolgt noch, da 4 Nietlöcher etwas zu groß sind und kleine Unterlegscheiben benötigen , die natürlich heute nicht da waren …..
Wenn das schöne Sommerwetter am nächsten Donnerstag noch vorhanden ist (soll so sein), werden wir wohl draussen arbeiten und das Bespannen der Querruder hoffentlich abschließen können. In der Werkstatt geht das nicht, weil der „Geruch“ des Klebelackes die Schüler und Schülerinnen stört….. Ist halt kein Parfüm, was sonst den Werkraum erfüllt, wenn Mädchen dort arbeiten …… nur für echte Holzflieger ist Spannlack Parfüm …. 🙂
29.08.2019
Heute war wieder ein sehr heißer Tag, den ich persönlich deswegen als unangenehm empfand. Der Körper verlangt nach Flüssigkeit, man trinkt, es ist angenehm im Hals und …………..man ist nassgeschwitzt. 😦
Das Vorhaben, das Bespannen der Querruder weiterzumachen, haben wir schnell aufgegeben, da es draussen für uns zu warm war.
Lasse und ich haben dann mit dem Vernieten der Kontur-Leisten weitergemacht. Die seitlichen Formleisten, auch die kürzeren im Cockpitbereich wurden angenietet. Mit den gestauchten Alunieten sieht das schon besser aus als mit Blindnieten (Poppnieten).
Einige Löcher in den Metallklammern waren zu groß. Da brauchten wir Unterlegscheiben … aber nicht die normalen …. dazu waren die Nieten nicht lang genug 😦 … Mit den inzwischen beschafften dünnen Passscheiben –> 0,3 mm dick, ging das dann sehr gut. Fa. Dunken in Braunschweig hat alles um das Thema Verschraubung. Dort bekommt man auch eine Schraube oder Scheibe einzeln, ohne Mondpreise zu zahlen …. Leider bekommen ich da aber die veralteten Alunieten zum Stauchen nicht .. :-((
Als wir dann heute uns auch noch an die Anbringung der oben zentral auf dem Rumpf befindlichen Leiste machten, mussten wir leider feststellen, dass wir von den dafür notwendigen längeren Nieten, bis auf 2 Stück, zuwenig hatten. Also neue bestellen und das bitte schnell bis zum nächsten Donnerstag …. ich schau mal im Internet……
Bilder zu unserer Aktion werden vielleicht morgen hier dazugestellt. Lasse muss die Bilder von seinem Smartphone noch rüberschicken.
Vergessen : Lasse hatte vor dem Vernieten noch zwei spezielle Holzleisten bearbeitet, die wir für die Komplettierung des Fußbodens vor dem hinteren Sitz benötigen.
Nächsten Donnerstag wird das Annieten der oberen Kontur-Leiste fortgeführt und verschiedene Verkleidungsteile aus Sperrholz dann an die Kontur-Leisten geklebt.
05.09.2019
Dank Internet konnten die fehlenden Nieten schnell beschafft werden.
Somit wurde heute die obere Formleiste des Rumpf fertig angenietet. Die Nieten sind echte Aluminiumniete zum Schlagen. Allerdings keine zum Bau von Metallflugzeugen, dazu sind sie zu weich. Das Annieten mit Hammer und Gegenmasse
Die angenietete obere Rumpfformleiste vor der Höhenleitwerksbefestigung. Das auslaufende Ende der Formleiste wurde dort auf die schon montierte Sperrholzplatte aufgeklebt.
Die auf dem Bild rechts zu sehende Leiste mit dem lockeren Tapestreifen,dient mit einer weiteren Leiste nur der Abstandshaltung, wenn der Rumpf an der Wand auf seine Gestell abgelegt wird. Die Formleiste würde sonst die Auflage bilden….nicht gut 🙂
Damit sind alle Formleisten fest montiert.
Lasse klebte um die hinteren Querkraftbolzen die vorbereiteten Sperrholzplatten. Die Platten dienen der Auflage der späteren Bespannung.
Wir haben dann noch die beiden Seitenwände im Cockpitbereich angeklebt und so alles stehen gelassen. Das soll nun in Ruhe aushärten.
Der Rumpf muss am Wochenende in einer Extraaktion wieder auf die Wandablage gehievt werden, da in der nächsten Woche die Werkstatt für den Werkuntericht der Schule benötigt wird.
Die Arbeit hatte heute wieder viel Spass gemacht. — > So konnte hinterher sichtbar betrachtet werden, was geschafft wurde :-)))
Nächste Woche ist ein Verputzen der Seitenwände, Weiterarbeit (Restarbeit) an den Sitzen, Bau der Instrumentenbretter und das Einpassen der hinteren Fußbodenteile angesagt …. Kleinkram also … muss aber auch gemacht werden.
———————————————————————————————————
Das zur Verfügung stehende Geld ist leider fast verbraucht. Über Spenden würden wir uns sehr freuen .
Das Spendenkonto für das Projekt wird von der Freien Waldorfschule Braunschweig e.V. geführt. Spendenbescheinigungen werden ausgestellt, wenn die Anschrift bekannt ist.
- GLS-Bank
- IBAN DE39 4306 0967 0015 9927 00
- BIC GENODEM1GLS
Alle Spenden bitte mit der Zweckbestimmung “Bergfalke” versehen und mir bitte auch mitteilen. —–> b.junker@daec.de DANKE
———————————————————————————————————————————
Weitere Arbeitspakete sind:
- Fertigstellung der Bespannung der Querruder
- Einbau von Kufe und Rad
- Fertigung neuer Sitze
- Fertigung der Instrumentenbretter
- Fertigstellung des Steuerungseinbaus
- Anbringen der Formleisten am Rumpf
- Fertigstellung der Kabinenhaube (Verglasung und Rahmenbleche)
- Fertigstellung der Cabriohaube
_____________________________________________________
_________________________________
_______________
______
_
Arbeiten in der Segelflugzeugwerkstatt des Braunschweiger Aeroclubs
Da für die Flügel kein Werkplatz in der Schule zur Verfügung steht, findet die Überholung der beiden Flügel in der Segelflugvereinswerkstatt vom Braunschweiger Aero Club im Weinbergweg statt.
_____________________________________________________
_________________________________
_______________
______
_
Arbeiten in der Heinrich-Büssing Berufsschule
- Fertigung von Beschlagteilen
- Fertigung von Verkleidungsblechen
- Heften der Fußpedalsteuerungsteile
- Entlacken von Fahrwerks- und Kufenteilen.
- Neubau des Radkastens
- Neubau der Fallschirmwanne vom vorderen Sitz.
23. Februar 2017:
Für das Heften der Rohre der Fußpedale der Seitenrudersteuerung steht uns das WIG-Schweißgerät in der Heinrich-Büssing Berufsschule zur Verfügung. Es sind fast alle Steuerungsteile geheftet und können bald autogen fertiggeschweisst werden. Die von den Schülern gefertigten Beschlagteile aus Blech, werden mit verbaut.
Links das geheftete hintere Seitensteuerungspedal mit den beiden auf richtige Distanz gebrachten Befestigungslaschen. Diese Laschen werden erst nach dem Verschweißen der Pedalrohre integriert. Rechts im Bild ein geheftetes Pedal vom vorderen Sitz. An beiden abgebildeten Pedalen fehlen noch weitere Teile zur Anbindung der Steuerseile.
28. Februar 2017
Das Anlenkteil für die Steuerseile der vorderen Pedale, das nach den Verschweißen, nach vorgegebenen Abständen ausgerichtet, angeheftet wird.
Alle Einzelteil sind nun geheftet und das erste Verschweißen kann beginnen.
Die Schmutzverkleidung des Rades hat wohl viel in ihrem Fliegerleben gelitten. Der mehrfach reparierte Radkasten wird in der Heinrich-Büssing Berufsschule nun neu gebaut. Da ist altes Handwerkswissen bei der Bördelverbindung der Bleche aufzuwärmen. Das wird lehrmäßig erstmal geübt….
14. März 2017
…….. und dann gebaut….. eine sehr schön gelungene Arbeit
Es war wohl eine lehrreiche und erfolgreiche Aktion. Herr Siegmann hat mit einigen Schülern nach Fertigung von diversen einfachen Hilfsvorrichtungen, einer Portion Nachdenkens und dem Einsatz von Zeit eine perfekte Verkleidung im Fertigungsstil des alten Radkastens von 1955 erstellt. Alte Handwerkskunst wurde hier praktiziert … immaterielles Kulturgut … wo werden heute noch mit derartigen Bördelungen Bleche individuell in Handarbeit zusammengefügt? Zur weiteren Anpassung der Verkleidung wurde die Holzkufe in die Berufsschule gebracht. In dem Schulprojekt findet eine wirklich sehr gute Kooperationsarbeit mit der Heinrich Büssing Berufsschule in Braunschweig statt. Einige restliche Beschlagteile wurden auch noch von Farbe befreit und werden demnächst lackiert.
_____________________________________________________
_________________________________
_______________
______
_
Der Anhänger
Die Überlegungen um die Beschaffung eines Transportanhängers werden wieder aufgenommen. Wenn der Rumpf weitgehend, bis auf das Bespannen und Lackieren, fertiggestellt ist, sollte ein sicherer und angepasster Anhänger zur Verfügung stehen.
Der Selbstbau wird nicht möglich sein, da dazu die Kapazitäten und die Räumlichkeiten fehlen.
Es soll ein Anhänger von einem Industrielieferanten passend für den Bergfalken gefertigt werden.
Die Beschaffung von Baumaterialien für den Industrieanhänger hat leider nicht so geklappt, wie wir uns das gewünscht hatten. Es wird also der „profane“ Weg des Erbetteln von Gelder für den Kauf beschritten. Wir wünschen uns dabei viel Glück und hoffen auf Zuspruch durch die angesprochenen Institutionen.
Die Seitenfläche des Anhänger bietet später die darstellende Möglichkeit der Information über das Projekt sowie deren Spender und Unterstützer.
Die angestrebte Version des Anhängers
_____________________________________________________
_________________________________
_______________
______
_
Ein Verein zum Aufbau, Erhalt und Fliegen von historischen Flugzeugen
Die Gründung eines Vereins oder/und einer Stiftung zum Erhalt und zum Fliegen von historischen Luftfahrzeugen in Braunschweig, ist als weiteres Ziel geplant. Es soll eine Struktur geschaffen werden, wo auch die schulische Ausbildung von Jugendlichen integriert ist.
Die Voraussetzung dazu ist es, einen geeigneten Werkraum für die Überholung historischer Flugzeuge sowie einen Hangar für die Unterstellung, errichten zu können.
Gesucht werden handwerklich und fliegerisch Interessierte, die an diesem Projekt mitmachen möchten.
–> Ich bitte um eine Kontaktaufnahme <–
Die Arbeiten am Erhalt von historischen Flugzeugen sind ein Weg, um das Wissen um das alte Flugzeugbauhandwerk am Leben zu erhalten. Es ist eine Spezies von immateriellem Kulturgut, was hierbei bewahrt wird und zum Erhalt des realen Kulturgutes Luftfahrzeug dient. Hierbei kann jungen Menschen das alte Handwerk vermittelt werden und für fachkundige Senioren und Rentner eine sinnvolle und befriedigende Tätigkeit sein, historische Flugzeuge flugfähig am Leben zu erhalten.
Zur weiteren Information über Ausbildung von Jugendlichen an der Wartung von Fluggeräten und dem Erhalt von historischen Flugzeugen durch Interessens-gemeinschaften, sei als Beispiel gerne auf folgende Adressen verwiesen:
http://www.jubi-ratzeburg.de/
https://fmh.club/
http://www.quax-flieger.de/
_____________________________________________________
_________________________________
_______________
______
_
>>>>>>> ZUSAMMENFASSUNG <<<<<<<<<<<
- Zur Lagerung des Rumpfes wurde ein Kran und Auflagestützen gebaut.
- Die Steuerungsteile und Formleisten wurden ausgebaut.
- Das Rumpfgerüst wurde entlackt und grundiert.
- Die Steuerungsteile wurden entlackt, grundiert und lackiert.
- Die Formleisten vom Rumpfgerüst wurden gereinigt und lackiert.
- Eine Vorrichtung zur Festigkeitsbestimmung von Holz wurde gebaut.
- Übungsrippen wurden hergestellt und zu Sektionen zusammengebaut.
- Die Flügel werden in der Werkstatt des Segelflugvereins restauriert.
- Eine Aufbewahrungskiste für die Haube wurde hergestellt.
- Die Kufe wurde überholt.
- Eine Bauhelling für die Cabrio-Haube wurde gefertigt.
- Eine ausbalanzierte Drehvorrichtungen für den Rumpf wurde gebaut.
- Das Rumpfgerüst wurde in einer Braunschweiger Lackiererei lackiert.
- Ein in der Lackiererei entstandener Schaden am Stahlrohrgerüst wurde behoben.
- Das Rumpfgerüst wurde an Mangelstellen und der Schadensstelle nachlackiert.
- Die Vorrichtungen für den Bau der Seitenruderpedale wurden gefertigt.
- Die Komponenten der Seitenrudersteuerung wurden gefertigt.
- Aufbewahrungskartons für die Leitwerke wurden gebaut.
- Übungen im Bespannen mit Stoff wurden durchgeführt.
- Die Steuerung wurde provisorisch montiert.
- Die Querruder wurden lackiert und zum Bespannen vorbereitet.
- Die Querruder wurden teilweise bespannt.
- Die Bugverkleidung aus Sperrholz und Blech wurde fertiggestellt.
- Die Bodenbretter für den hinteren Sitz wurden gefertigt.
- Die Störklappenrahmen wurden lackiert und mit Holzteilen zur Befestigung der Abdeckplatten ausgestattet.
- Die Störklappenabdeckplatten wurden gefertigt.
- Die Rohre für den Grundrahmen der Cabriohaube wurden zugeschnitten.
- Die Bauteile für die Sitze werden derzeit gefertigt.
- Die Sitze sind fertig.
- Die Konturleisten sind am Rumpf angebracht.
_____________________________________________________
_________________________________
_______________
______
_
Das zur Verfügung stehende Geld ist fast verbraucht. Über Spenden würden wir uns sehr freuen .
Das Spendenkonto für das Projekt wird von der Freien Waldorfschule Braunschweig e.V. geführt.
- GLS-Bank
- IBAN DE39 4306 0967 0015 9927 00
- BIC GENODEM1GLS
Alle Spenden bitte mit der Zweckbestimmung “Bergfalke” versehen und mir bitte auch mitteilen. —-> b.junker@daec.de DANKE
_____________________________________________________
_________________________________
_______________
______
_
Schauen Sie bitte mal wieder rein, über Fortschritte und neue Informationen wird kontinuierlich berichtet.
Die Technik gibt es her, dass täglich gesehen werden kann, wieviel Besuche auf diesem Blog gemacht wurden und aus welchem Land der Erde diese kommen.
Bis jetzt haben sich neben den hiesigen Interessierten aus 41 Ländern, Besucher diesen Blog angesehen. Von Russland, Finnland, Norwegen, Schweden, Dänemark, Malta über Äthiopien bis nach Südafrika, von Kanada, USA über Kolumbien, Argentinien bis Chile, dann aus Indien, Südkorea, China, Japan über Australien bis nach Neuseeland und aus fast allen europäischen Staaten werden Besuche mehrfach registriert.
Besonders aus der Slowakei wird diese Internetseite regelmäßig besucht …. 🙂
Vielen Dank für Ihr Interesse
Über Kommentare im Blog und Unterstützung jeglicher Art würden wir uns sehr freuen. Bitte schreibt uns ….. DANKE
Verantwortlich für Text und Projekt : Bernd Junker b.junker@daec.de Dokumentationsstand 15.12.2019